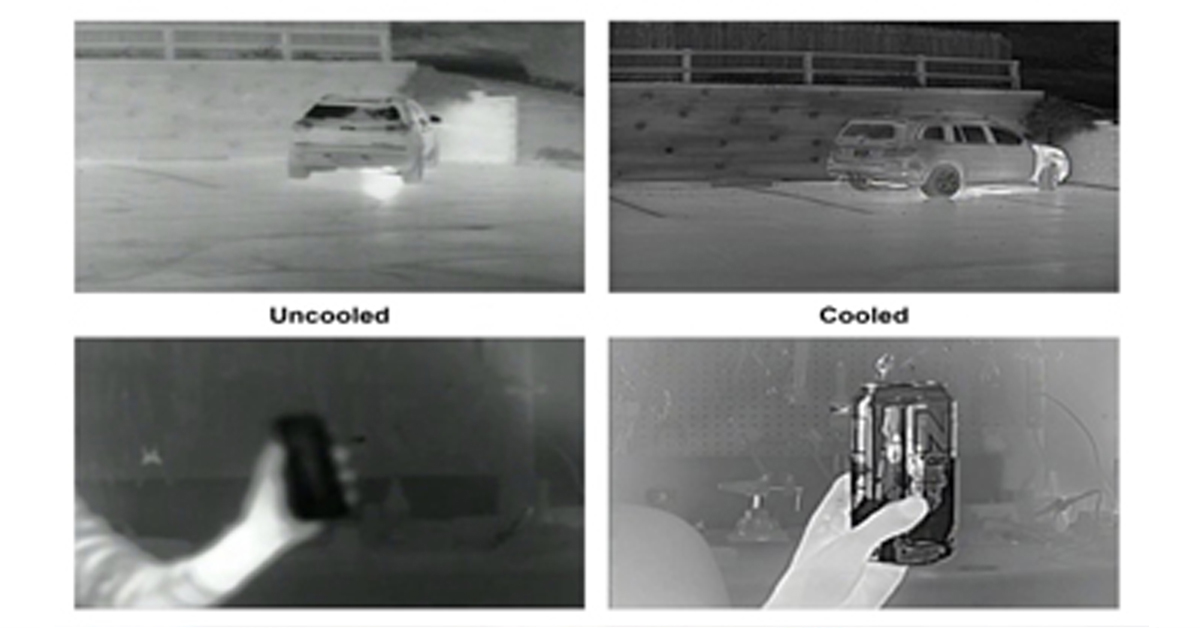
Battery Inspection Using Advanced Thermography
Battery Inspection Using Advanced Thermography
Anatomy of a Lithium Ion Battery
A lithium ion battery consists of multiple parts in which the cell acts as the primary component. The cell is the horsepower of the battery and consists of the following materials:
Current Collectors : Current collectors are two battery ends with positive and negative connection points. These ports are used to charge (absorb power) and discharge (drain power) the battery.
Cathode : The cathode is a positive electrode made of a chemical compound metal oxide and stores lithium.
Anode : An anode is a negative electrode that is typically made of carbon which stores lithium.
Separator : The separator restricts the flow of electrons inside the battery, but allows lithium ions to pass back and forth through the cathode and anode electrodes.
Electrolyte : The electrolyte fills between the electrodes and transports lithium ions from the anode and cathode during charging and decharging.
Lithium ion Battery Operation
The operation of a lithium-ion battery is related to the back and forth movement of lithium ions between cathode (+) and anode (-) electrodes. Ions move in one direction during charging and in the opposite direction during discharge. When the battery is fully charged or discharged, the ions no longer flow.
Charging Phase (Suction Power)
During the charging stage, when external power is applied, the lithium ions will pass from the positive cathode to the negative anode through the separator and electrolyte. At the same time, electrons will flow from the cathode to the anode, but unlike lithium ions, electrons cannot pass through the separator and take a different path around the external circuit. Electrons and ions coming to the anode combine. The battery is fully charged and ready for use when no more ions can flow.
Discharge Phase (Power Supply)
During the discharge phase, the lithium atoms in the anode are ionized and separated from their electrons. Lithium ions pass through the separator and electrolyte from the negative anode to the positive cathode. Simultaneously, free electrons flow from the anode to the cathode electrode through the external circuit and provide power to an external device such as a laptop computer. Ions and electrons recombine at the cathode, becoming electrically neutral. When no more ions can flow, the battery is completely discharged and needs to be charged to power up again.
Lithium ion Battery Production Process
The graph below shows the battery manufacturing process, which consists of three main parts: electrode preparation, cell assembly and battery electrochemical activation.
1. Slurry Preparation:
The active substance (AM), the conducting substance and the binder are mixed with the solvent to form a homogeneous slurry.
2. Coating and Drying:
The slurry is pumped into a slot mold, coated on both sides of the current collector (Aluminum foil for the cathode and copper foil for the anode) and transmitted to the drying equipment to evaporate the solvent.
3. Calendering:
The electrodes are compressed by passing them through a two-cylinder press. This means that the physical properties of the electrodes (bonding, conductivity, density, porosity, etc.) will help to adjust.
4. Cutting Electrodes:
The finished electrodes are stamped and cut to the required size to fit the cell design. The electrodes are then sent to the vacuum furnace to remove the excess water.
5. Cell Assembly:
After the electrodes are thoroughly prepared, they are sent to the dry room with separators for cell production. The electrodes and the separator are wrapped or stacked layer by layer to form the internal structure of a cell. Aluminum and copper tabs are welded to the cathode and anode current collector, respectively.
6. Electrolyte Filling and Formation:
The cell stack is then transferred to the designed enclosure. Manufacturers use various packaging depending on the cell application. The enclosure is filled with electrolyte before the final sealing and completes the cell production.
Battery/Electrode Performance
At a basic level, any factor that affects the movement of lithium ions between cathode and anode electrodes within a battery will affect the performance of that battery. Therefore, the design, manufacture and operation of a battery should be to optimize the flow of ions and electrons.
In the production process, there are situations when defects may enter the product (battery). For example, during the Coating and Drying step, the forming electrodes become potentially sensitive to the following:
- Uneven compound spread / change of thickness
- Change in the ratio of carbon to polymer binder
- Scratches
- Air bubbles / puffiness
Other factors that harm performance may be caused by the ingress of contamination particles into the electrode foils. During the coating, polishing and cutting stages, electrode foils may be exposed to stratified particles, corroded metallic particles and dust in the production environment.
The first encountered pollutants and defects will negatively affect the ability of the ion /electron to move within the electrochemical cell, thereby reducing the battery performance.
Advanced Thermography for Battery Inspection and Quality Control
IR Thermography has been shown to be an effective non-destructive testing method for quality control in multiple industries for a variety of applications. The basic operation of an IR camera is based on the principle of heat transfer of radiation. The infrared camera has an array of focal plane detector elements inside it that “see” the infrared light emitted from the object surfaces. The radiation captured by the infrared camera detector is digitized, converted into data and displayed as an image that can be viewed in the visible spectrum. Some infrared cameras are radiometrically calibrated to record and display units of measurement. Infrared cameras with different sensors and pixel resolutions are available to see certain infrared wave bands.
Flash Thermography for Battery Inspection
Battery Inspection using Active Thermography involves stimulation of the target and has been found to be the most effective in the detection of defects and disruptors of battery electrodes. Flash IR thermography is a form of active thermography in which the target is subjected to a flash of thermal energy, and then the change in surface temperature is monitored by an IR camera. A thermal wave signal sequence is obtained by a computer with real-time image signal processing and analysis, which reveals how thermal energy passes from the surface into the target. If there are gaps or defects in the target, the thermal conduction paths are disrupted. These distortions lead to temperature differences on the surface, which are detected by IR thermography.
Blog Posts
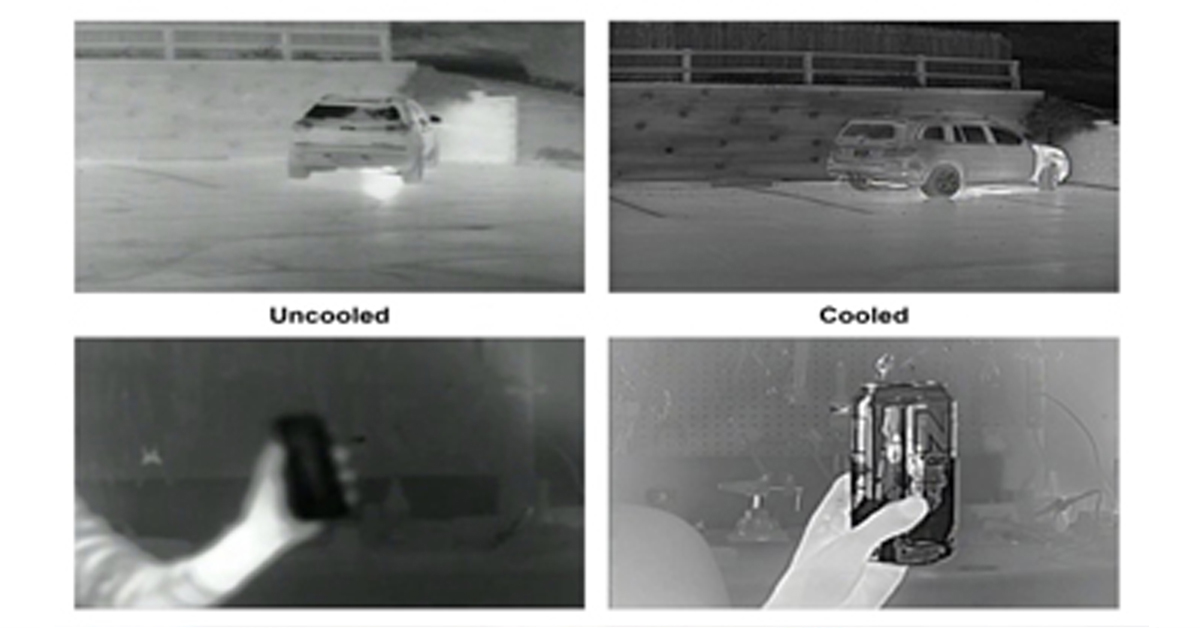
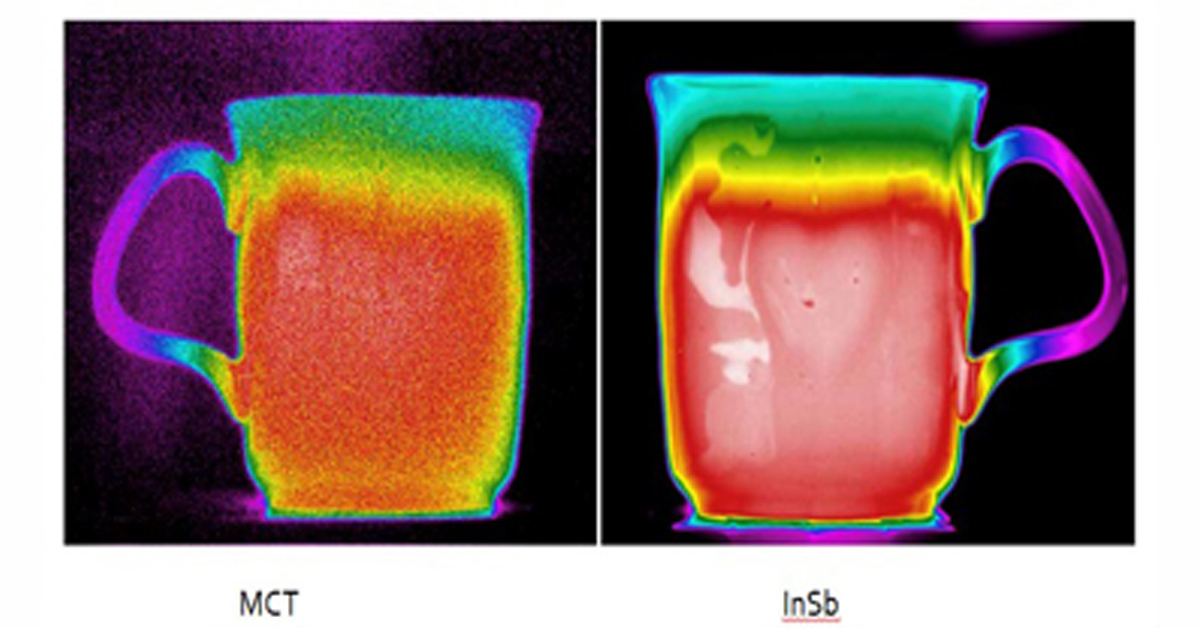
Thermal Camera Selection
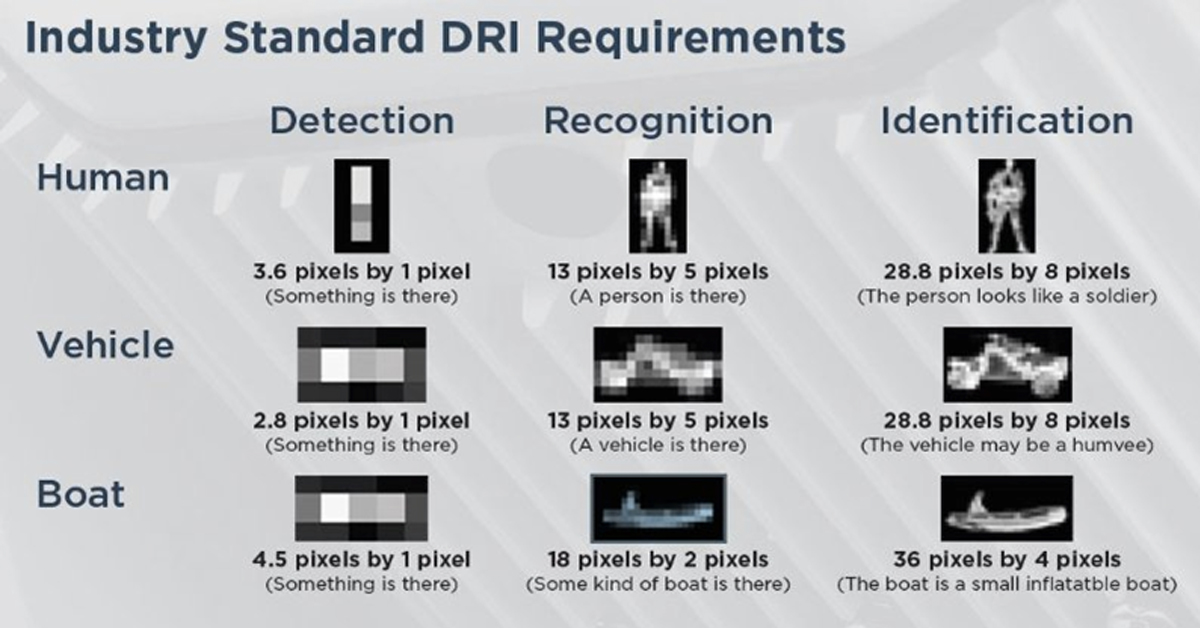
How Far Can I See?
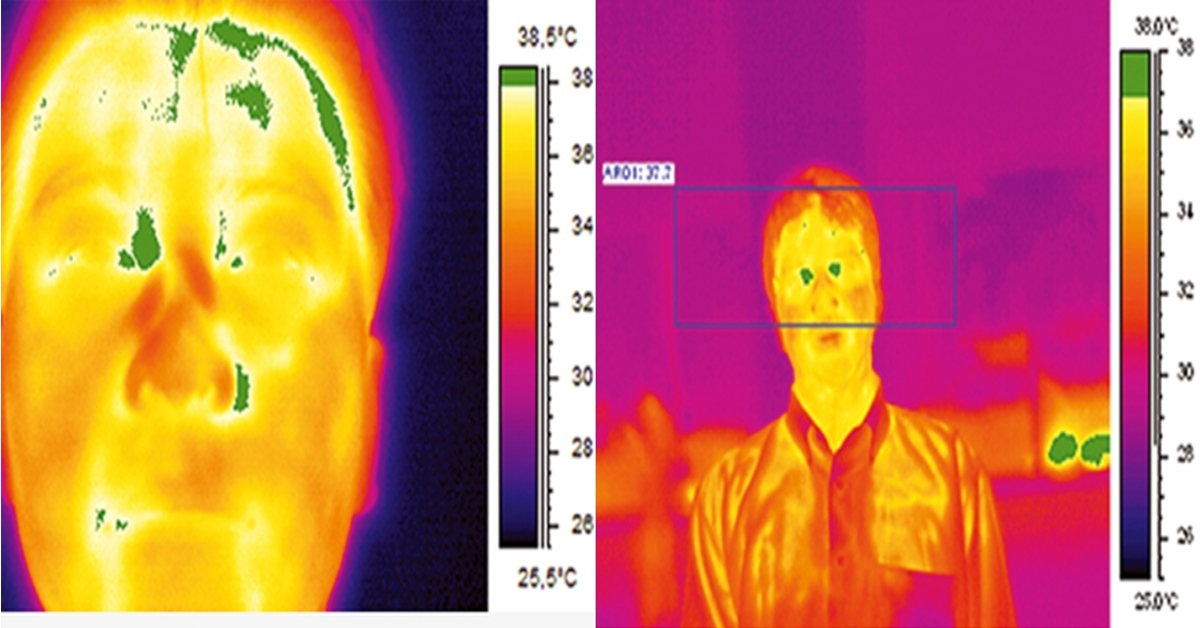
How Should Human Temperature Be Measured?
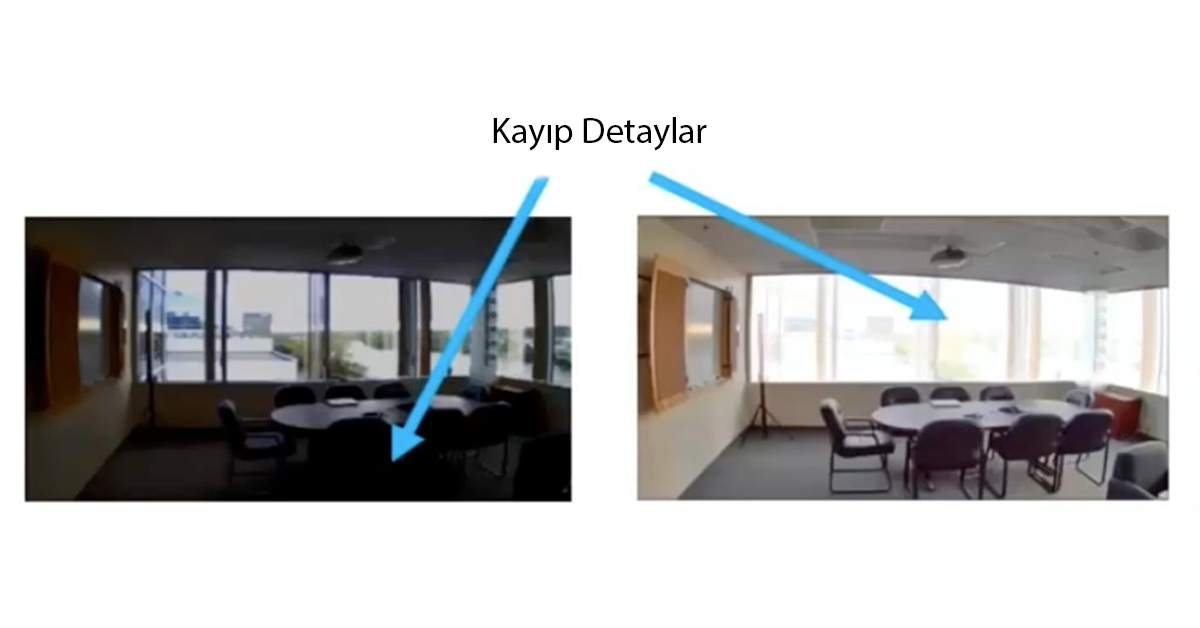
What is Wide Dynamic Range?
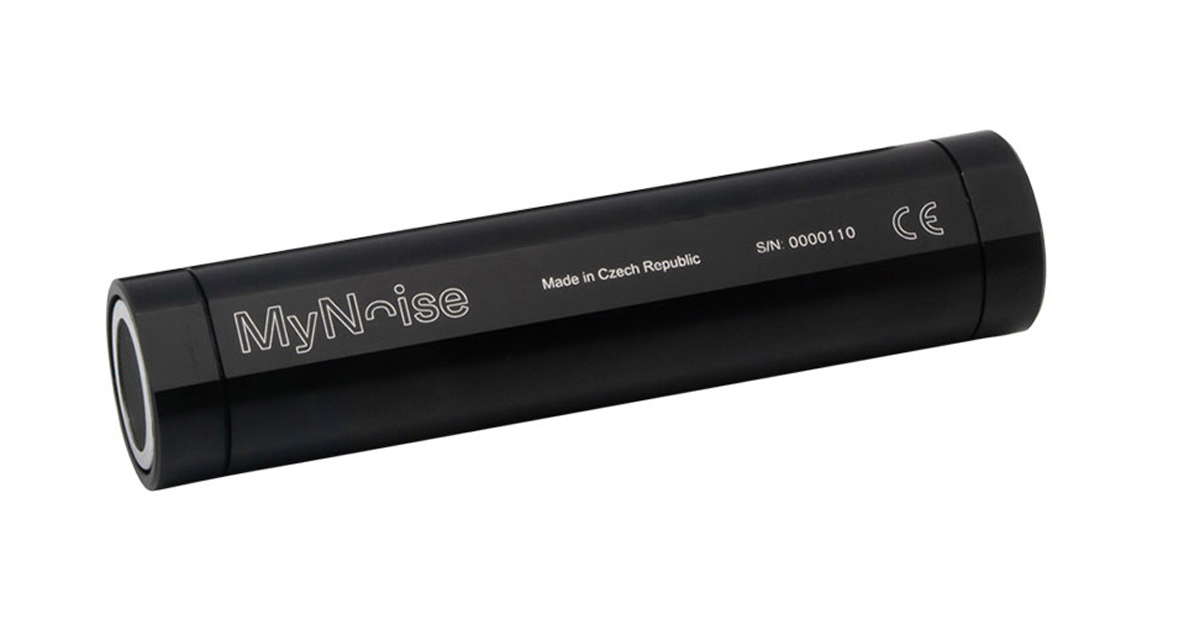
MYNOISE AUDIO MIXER REVIEW
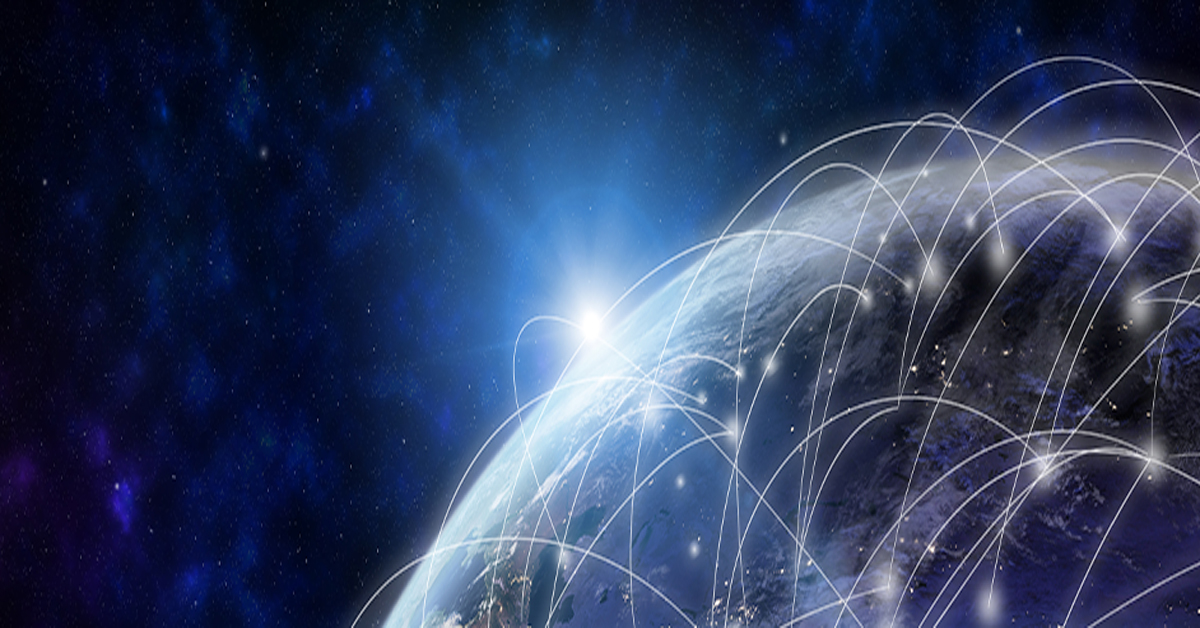
WHAT IS A WIRELESS DISTRIBUTION SYSTEM?
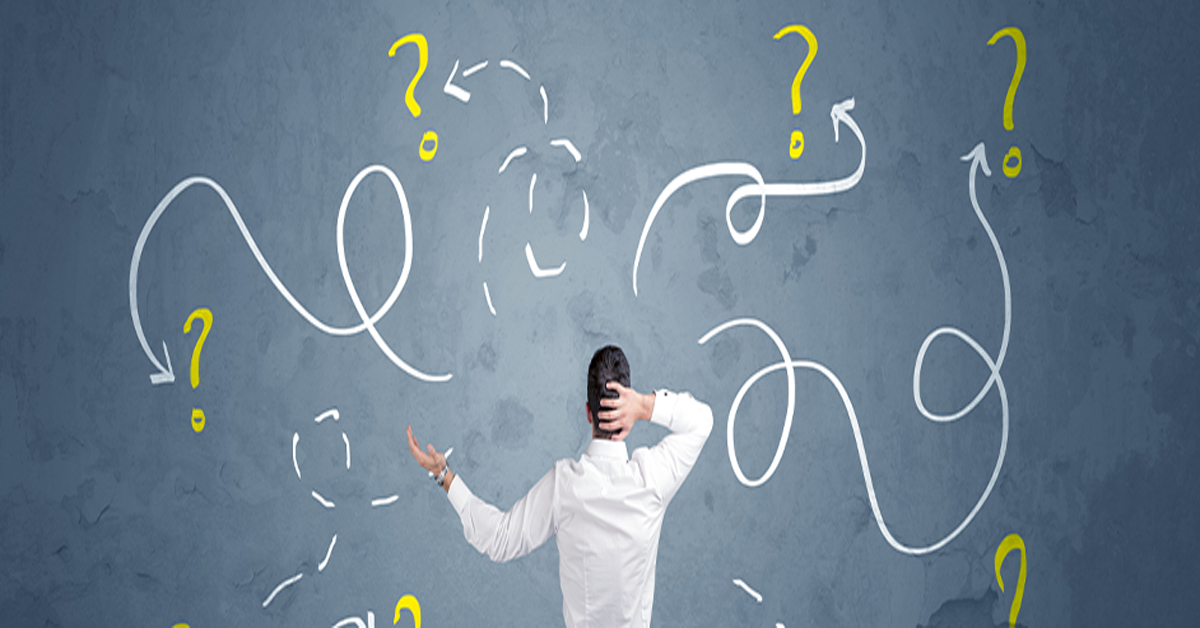
POE VS. POE+ VS. POE++: CHOOSING THE RIGHT INDUSTRIAL ETHERNET SWITCH FOR YOU
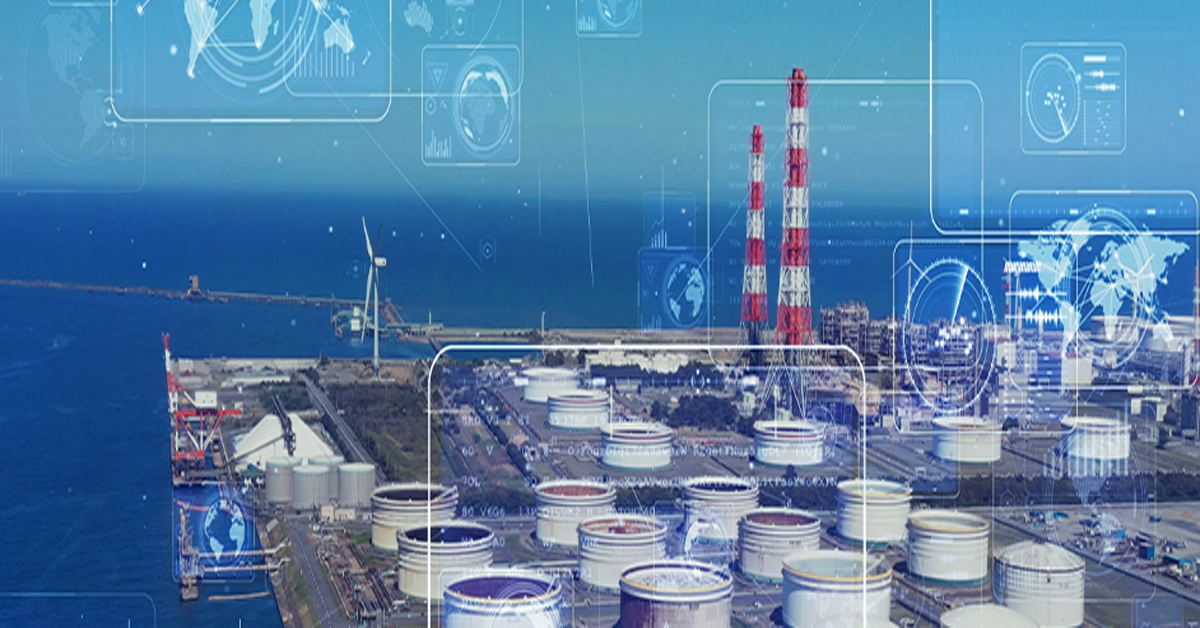
INDUSTRY-LEADING INDUSTRIAL ETHERNET SWITCHES
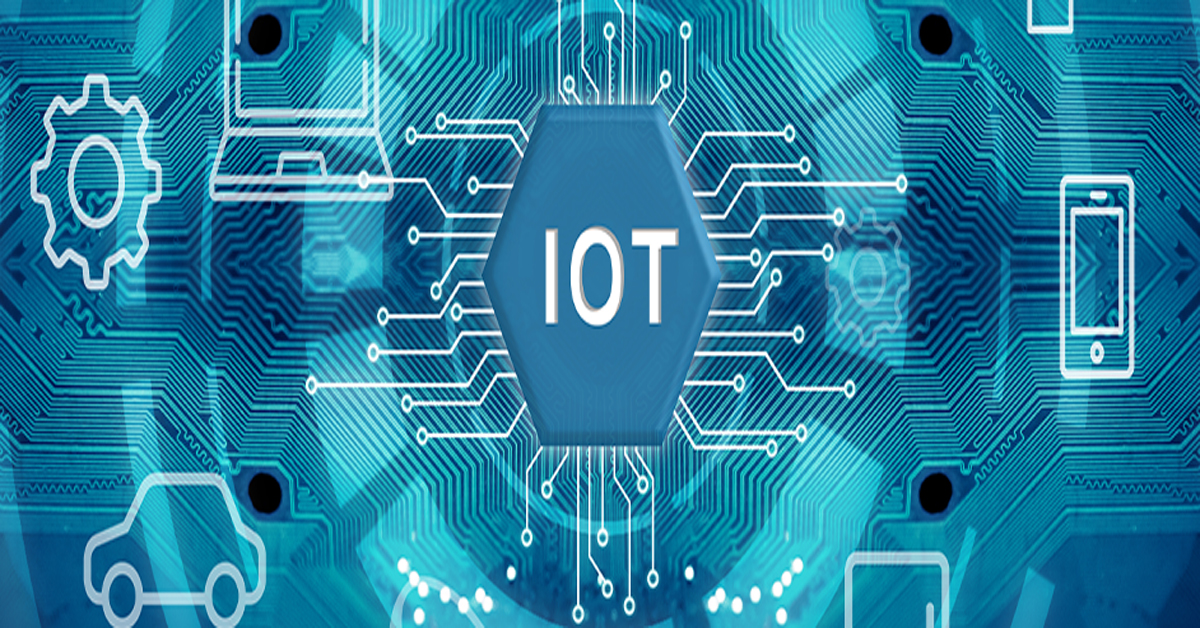
UNDERSTANDING WHAT THE INDUSTRIAL INTERNET OF THINGS IS
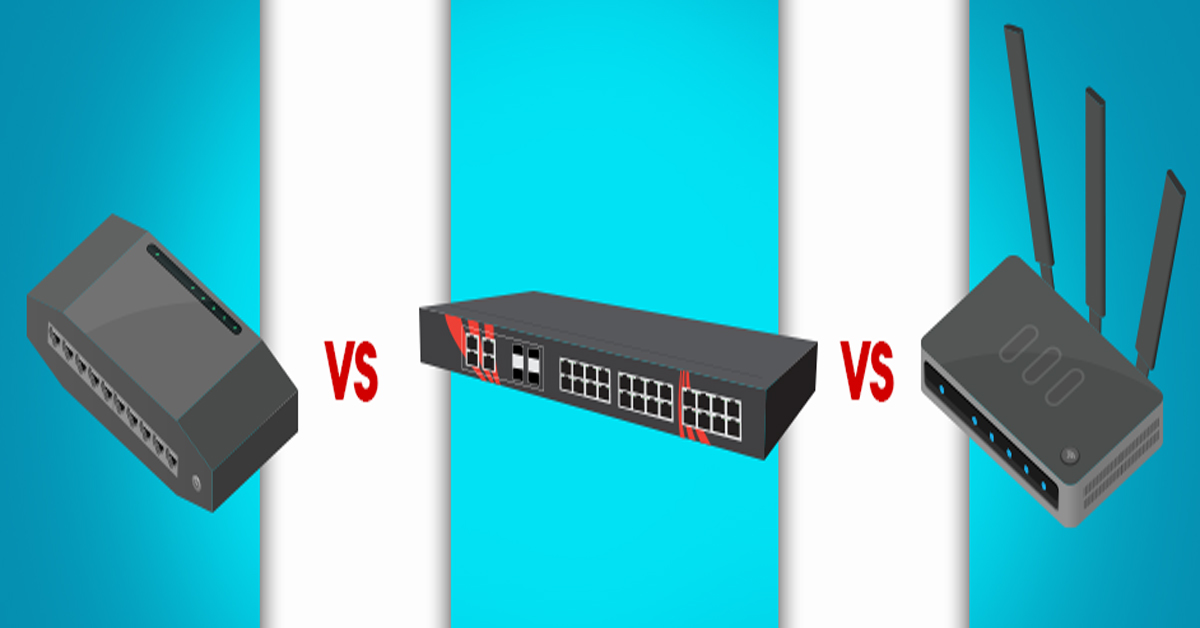
THE DIFFERENCE BETWEEN A HUB, SWITCH, & ROUTER
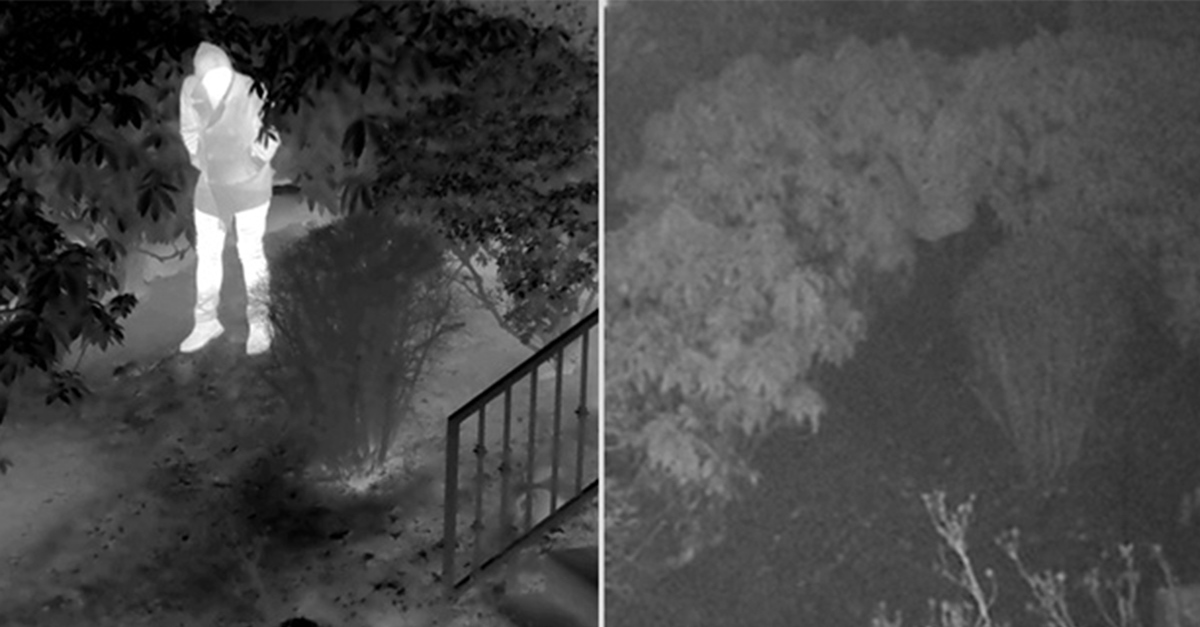
5 Benefits of Thermal Imaging Cameras
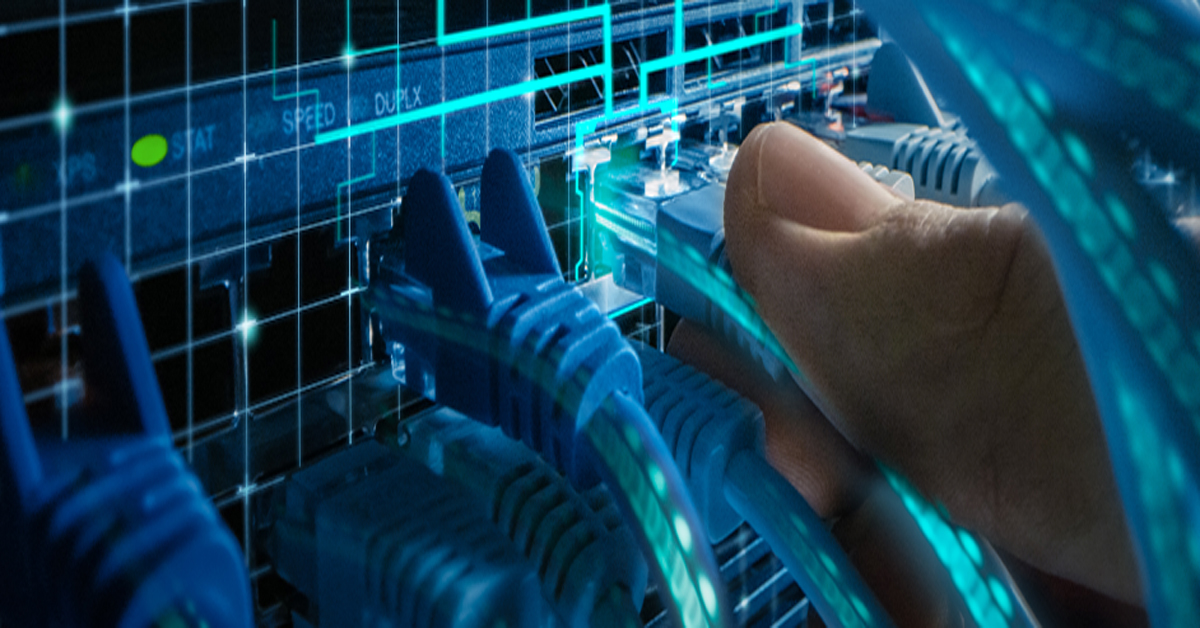
DIFFERENCE BETWEEN INDUSTRIAL ETHERNET AND REGULAR ETHERNET
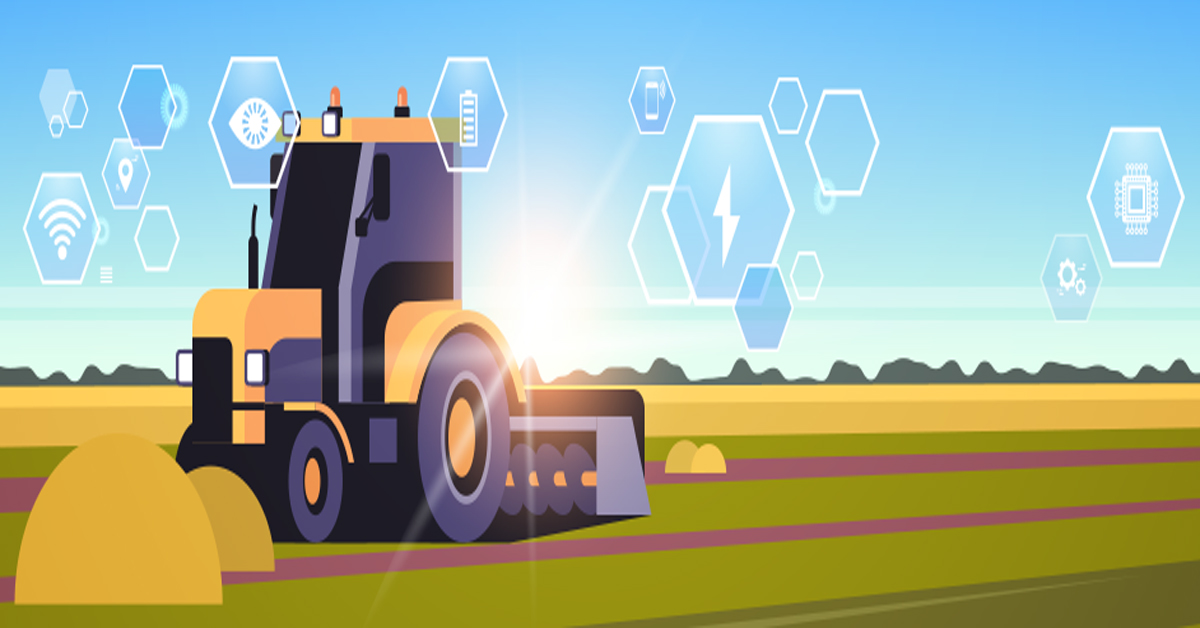
INDUSTRIAL NETWORKING EQUIPMENT USED FOR AUTONOMOUS VEHICLES
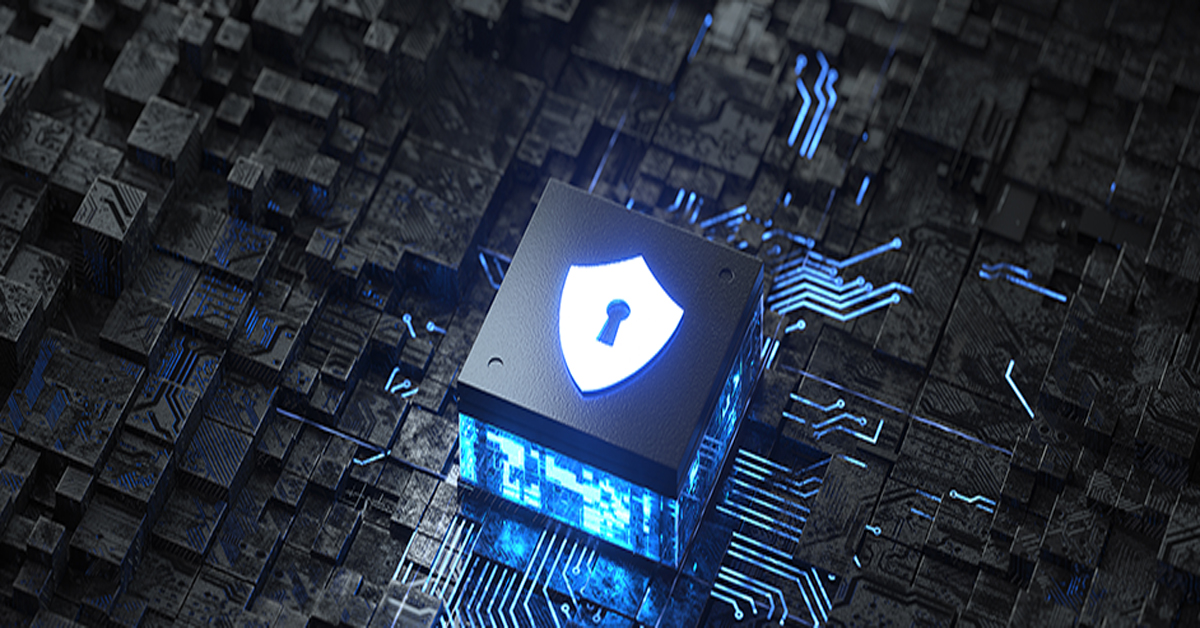
CYBERSECURITY: PROTECTING INDUSTRIAL CONTROL SYSTEMS
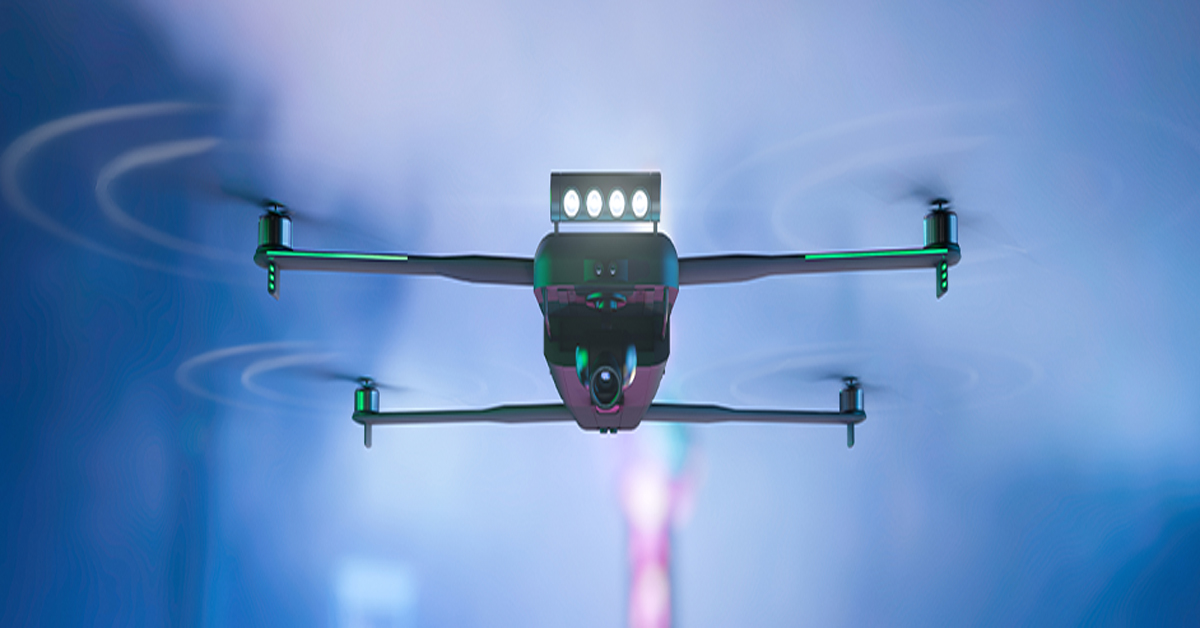
HOW INDUSTRIAL NETWORKING CAN PROVIDE SECURITY FROM DRONES
.webp)
Thermal Cameras Reveal How to Keep Your Home Cool During a Heat Wave
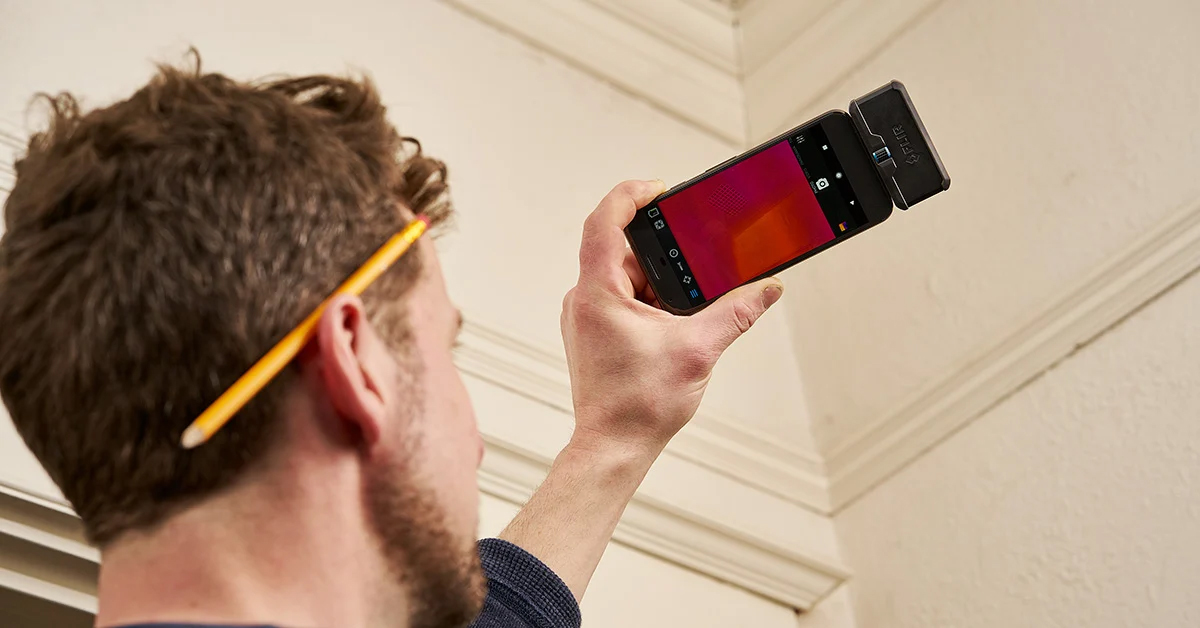
FLıR ONE PRO
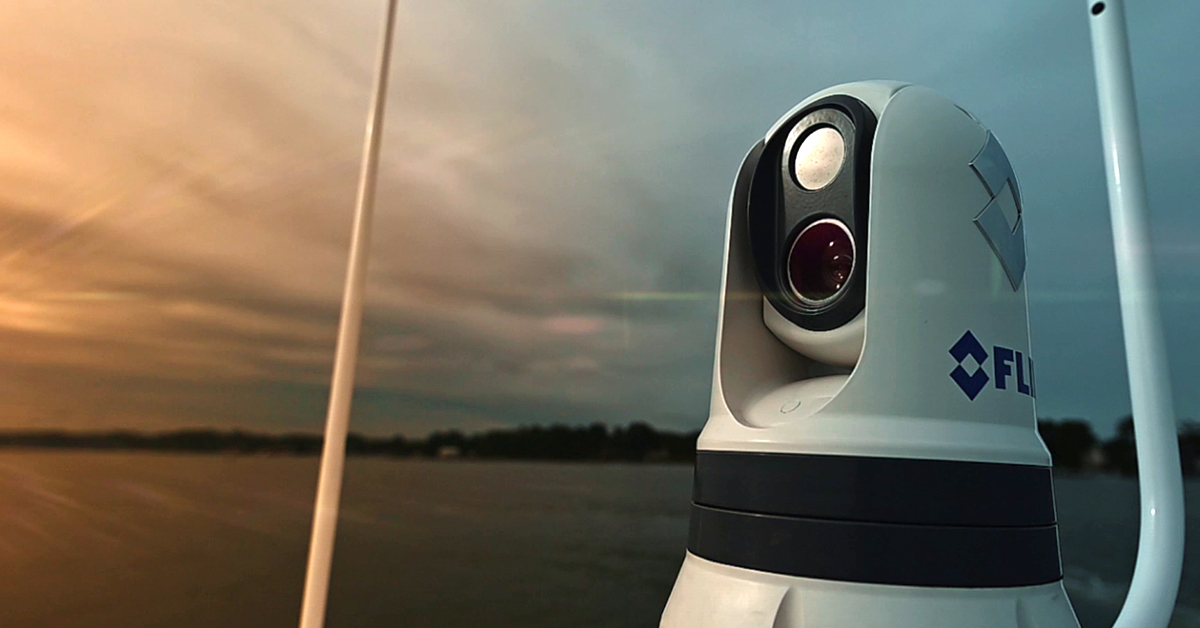
On the Water with the FLIR M364C
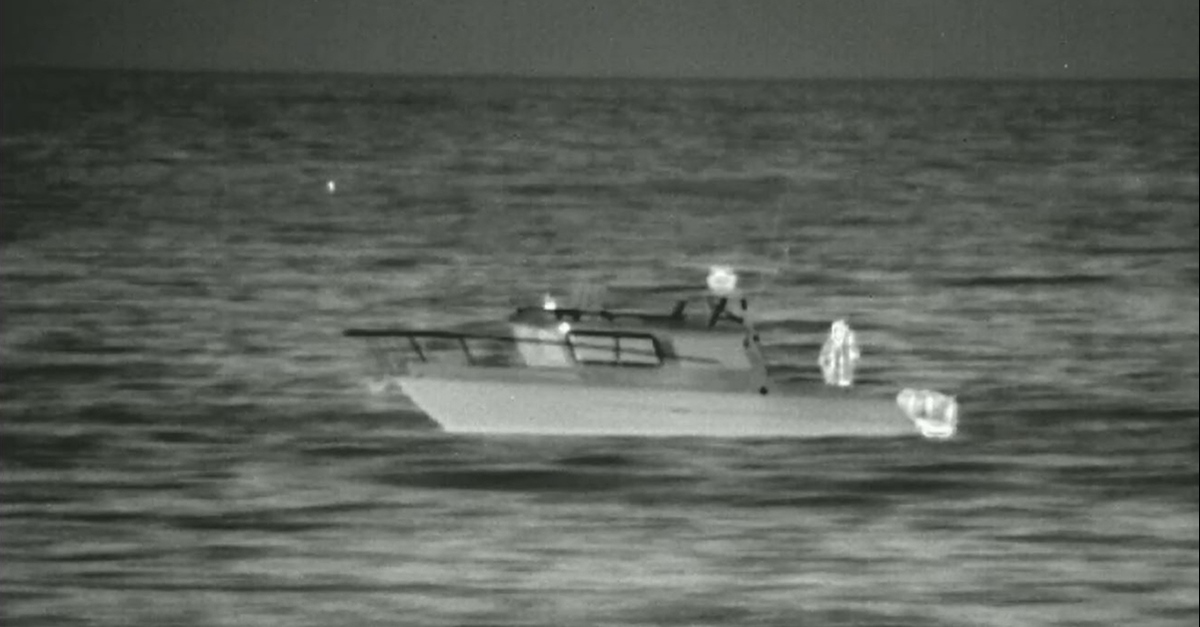
Unmatched Maritime Awareness with Cooled Thermal Imaging
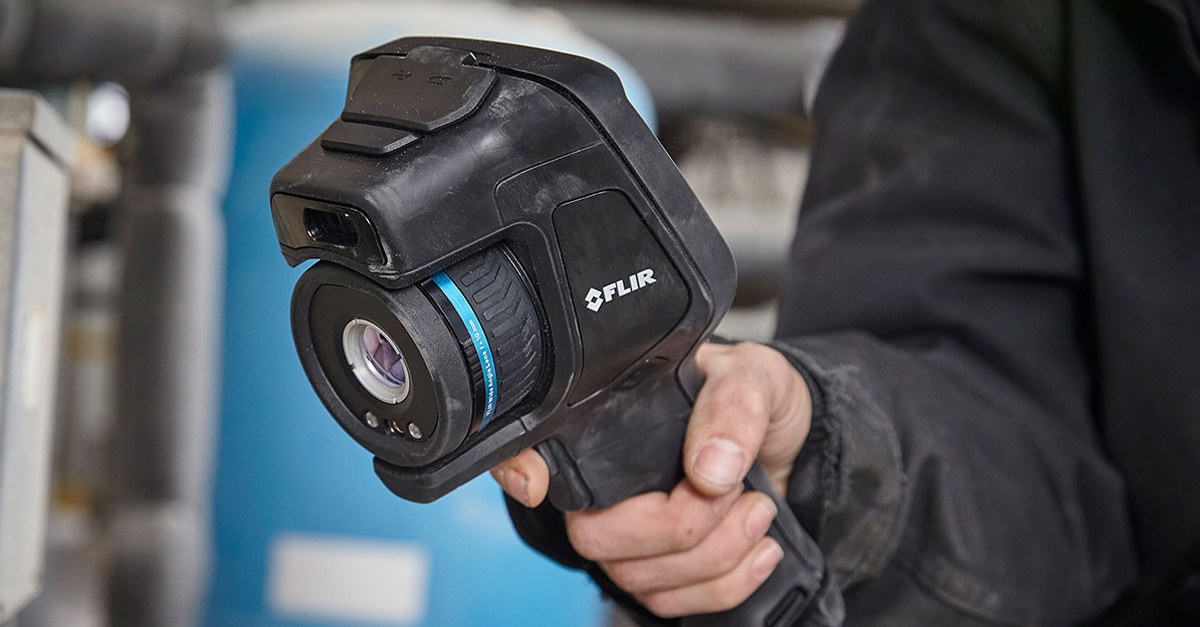
What Is the Right Handheld Thermal Camera for You?
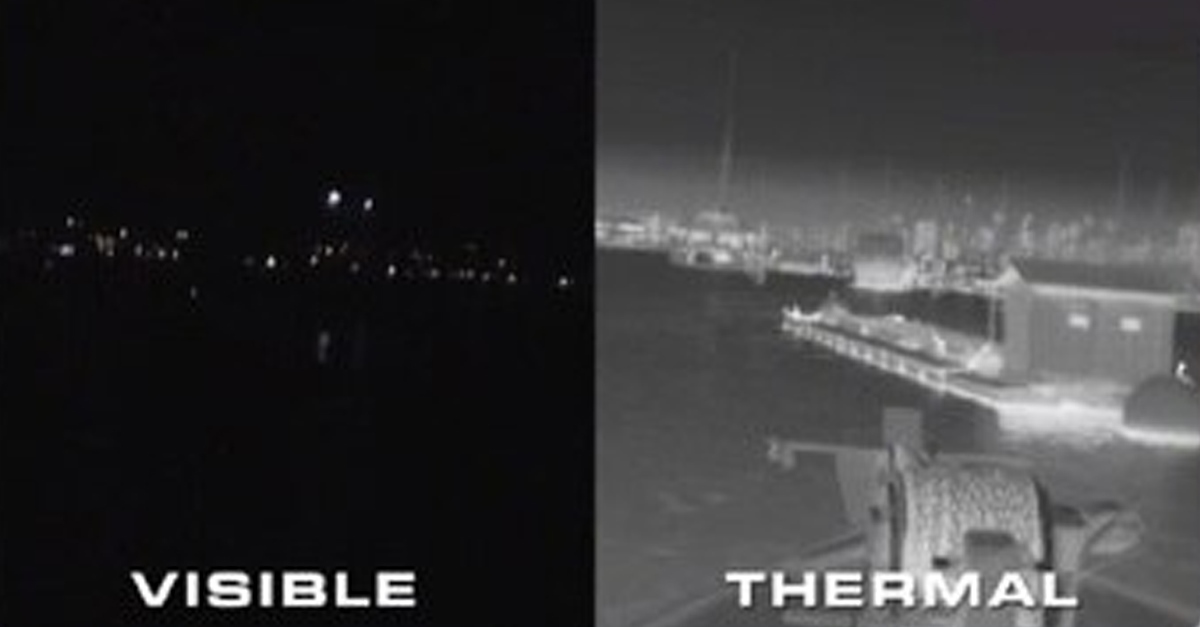
Camera Resolution and Range
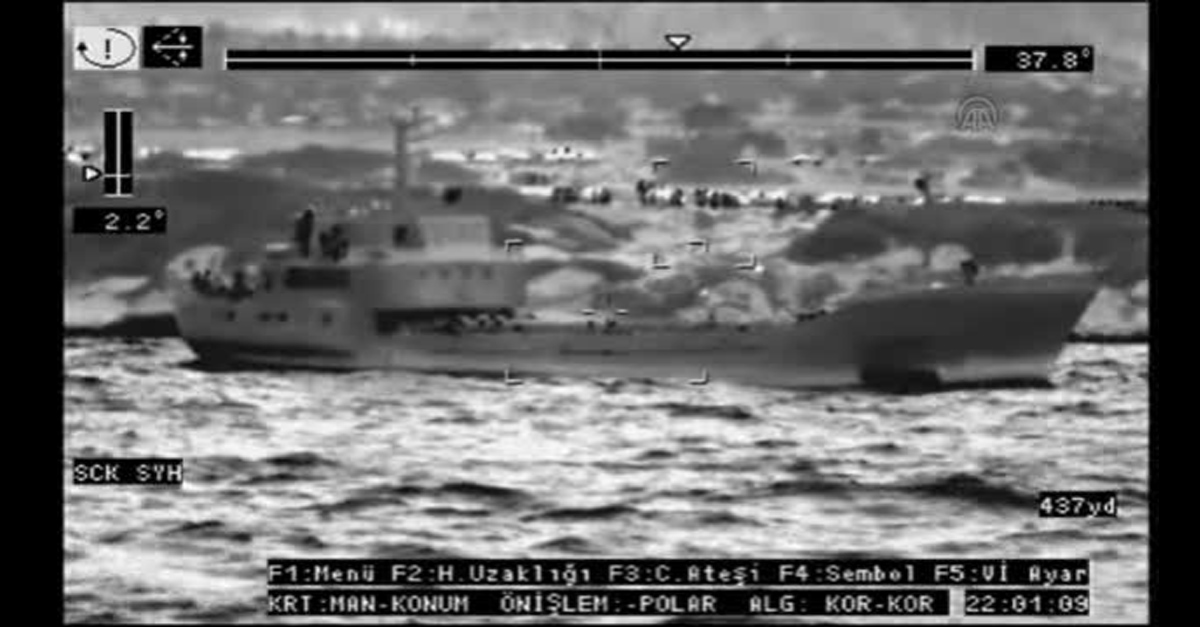
Special Applications for Marine Cameras
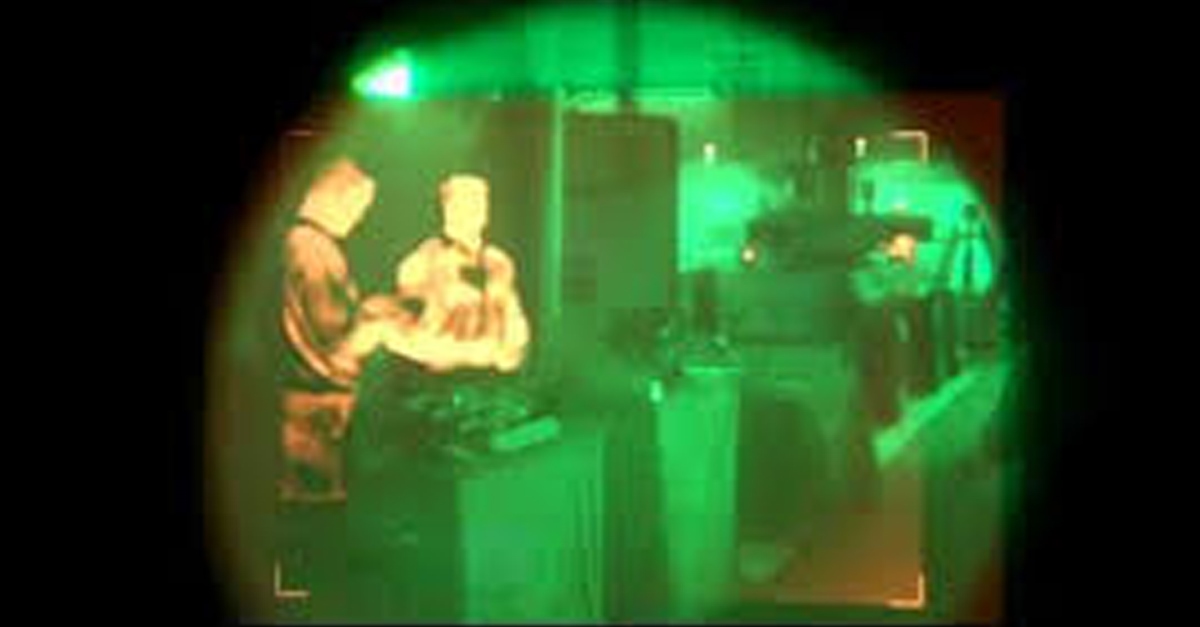
What’s The Difference between Thermal Imaging and Night Vision?
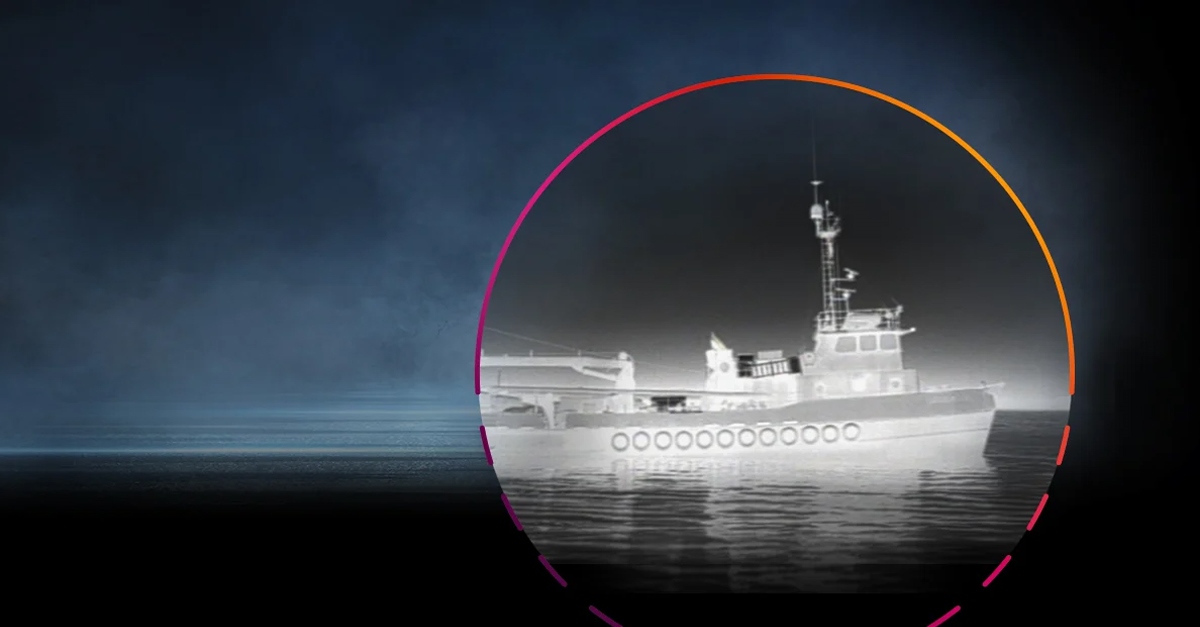
Can Thermal Imaging See Through Fog and Rain?
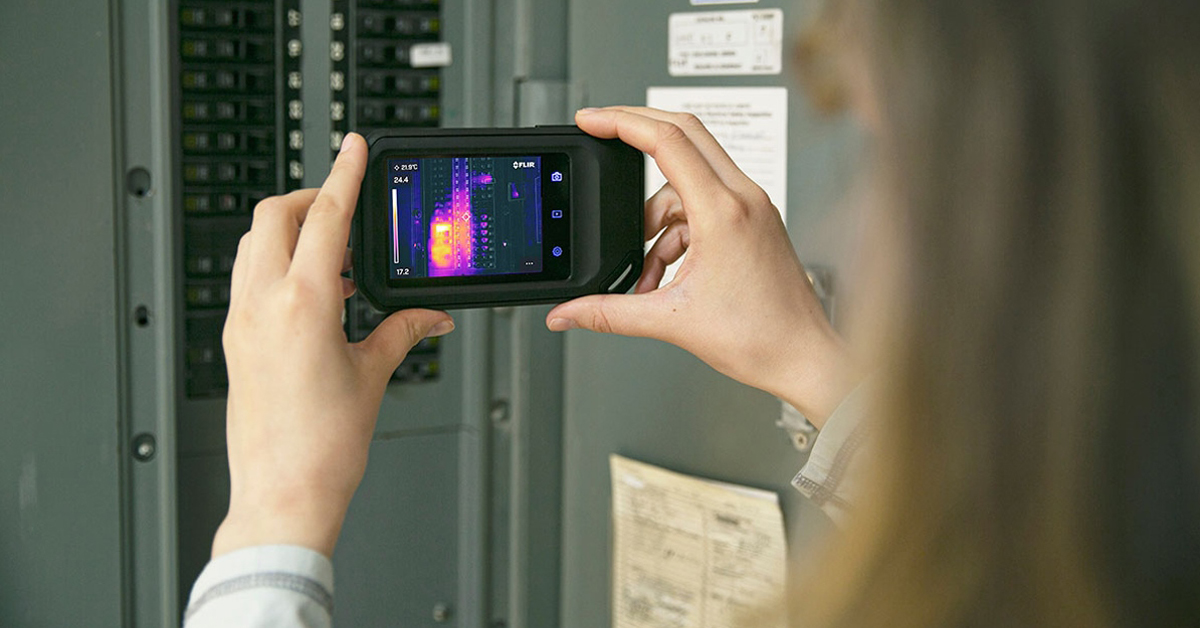
Which Cx-Series Camera Is Right for You?
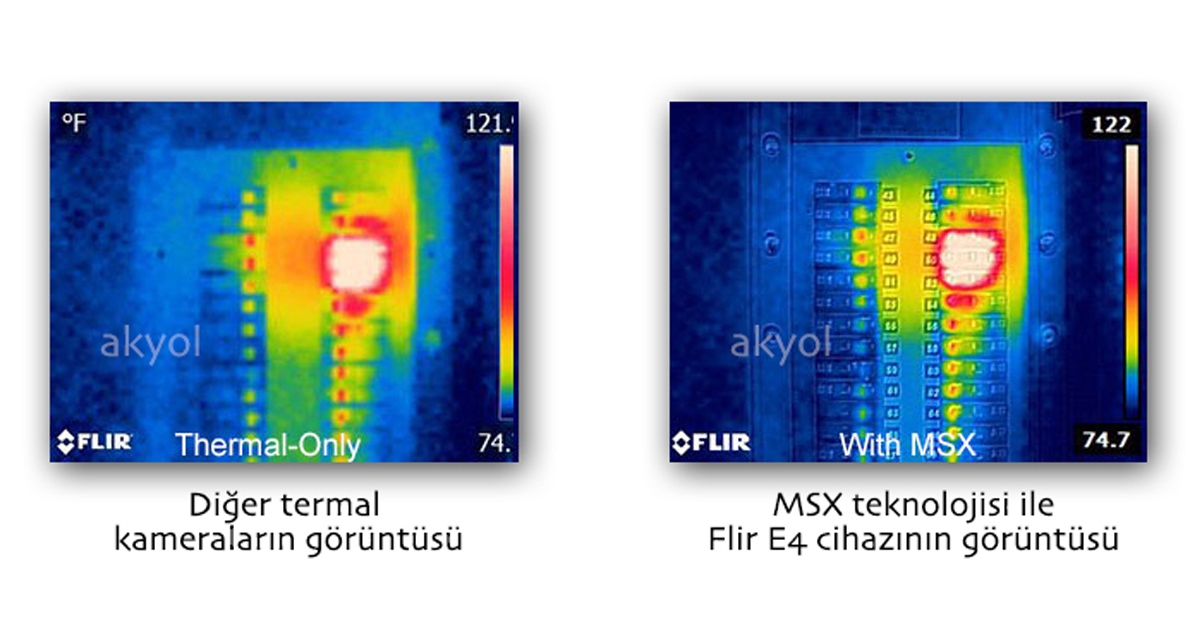
What is MSX®?
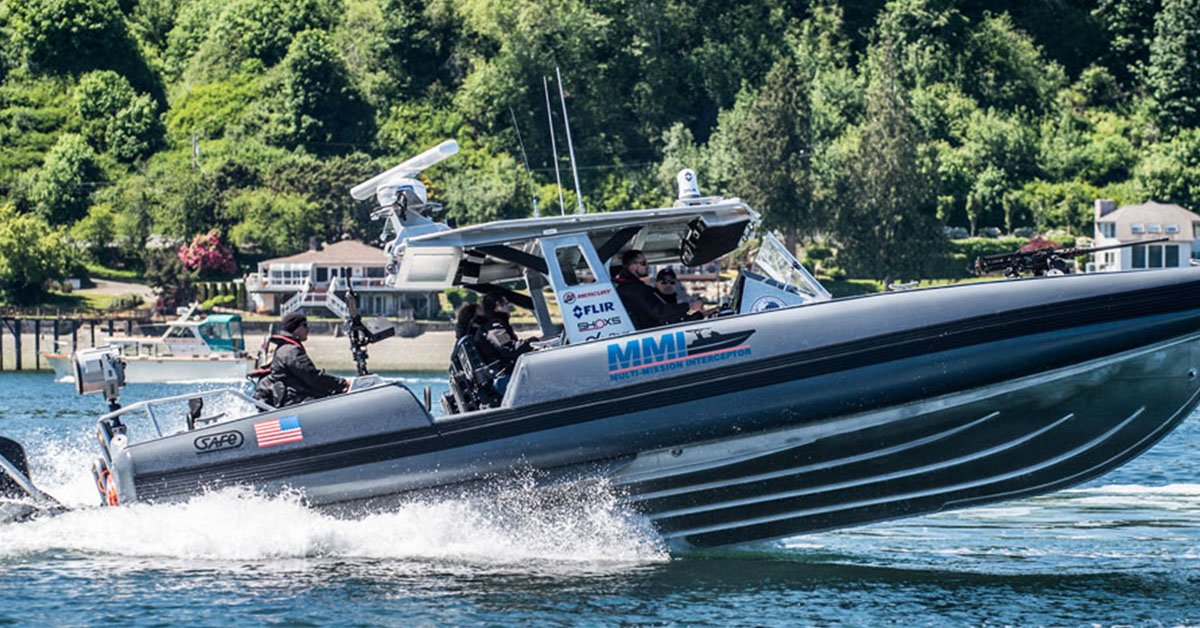
Five Reasons Maritime First Responders Need Thermal Imaging
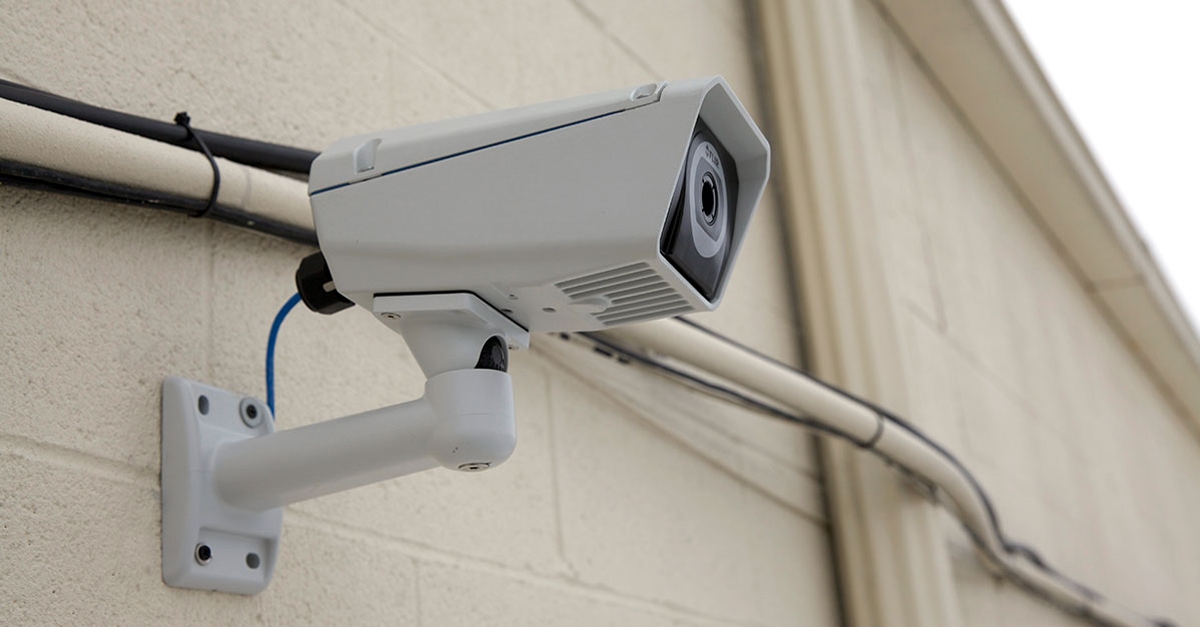
3 Distinguishing Features of Superior Thermal Cameras
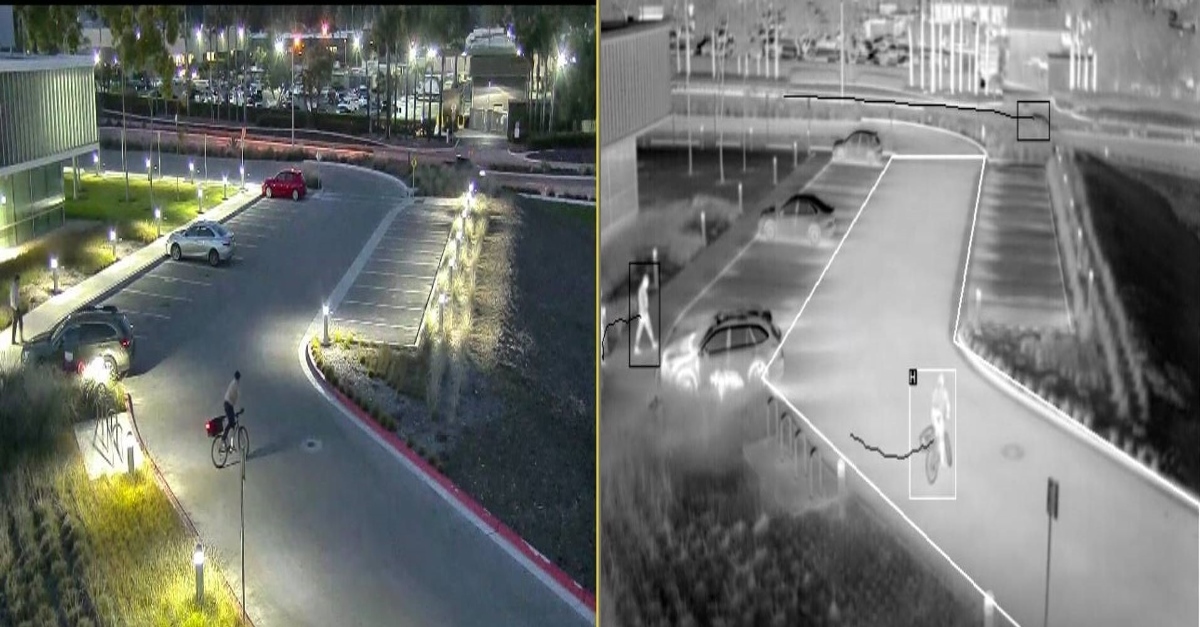
Determine Which Visible and Thermal Security Cameras You Need

Bullet vs. PTZ vs. Dome: Which Security Camera Is Right for You?
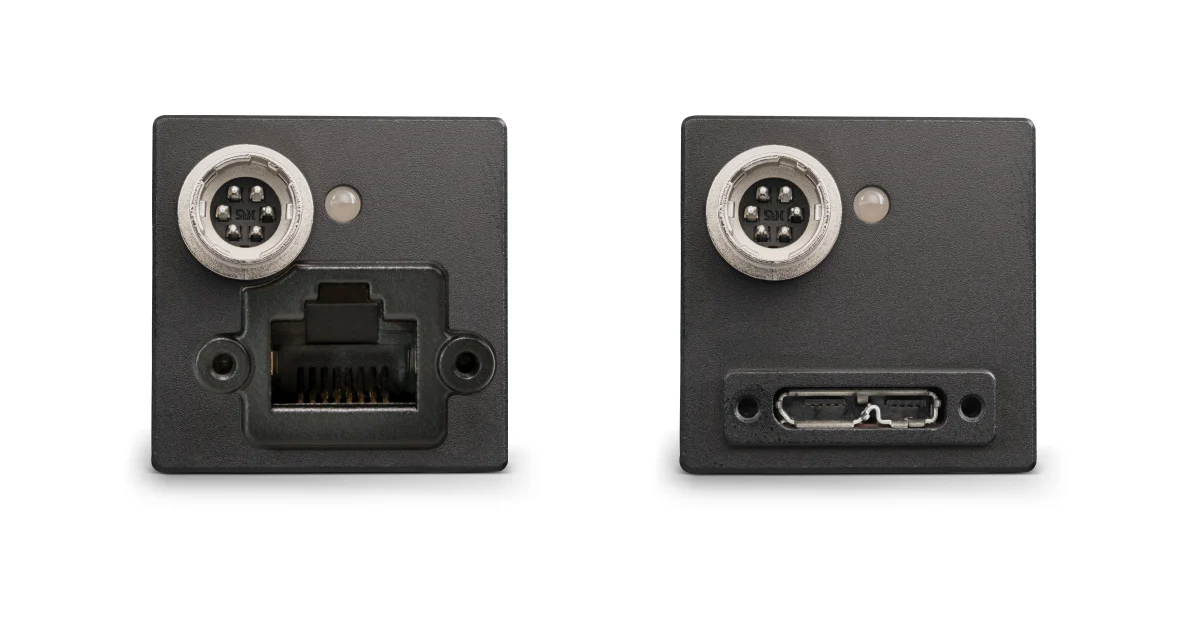
Interfaces for Machine Vision
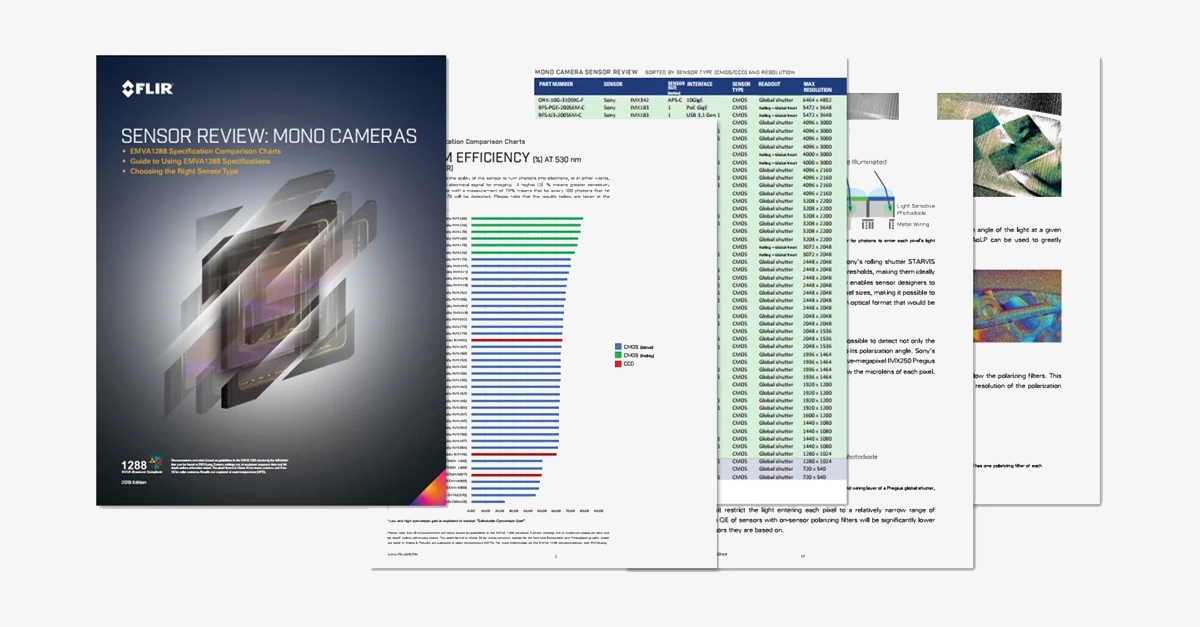
Machine Vision Sensor Review
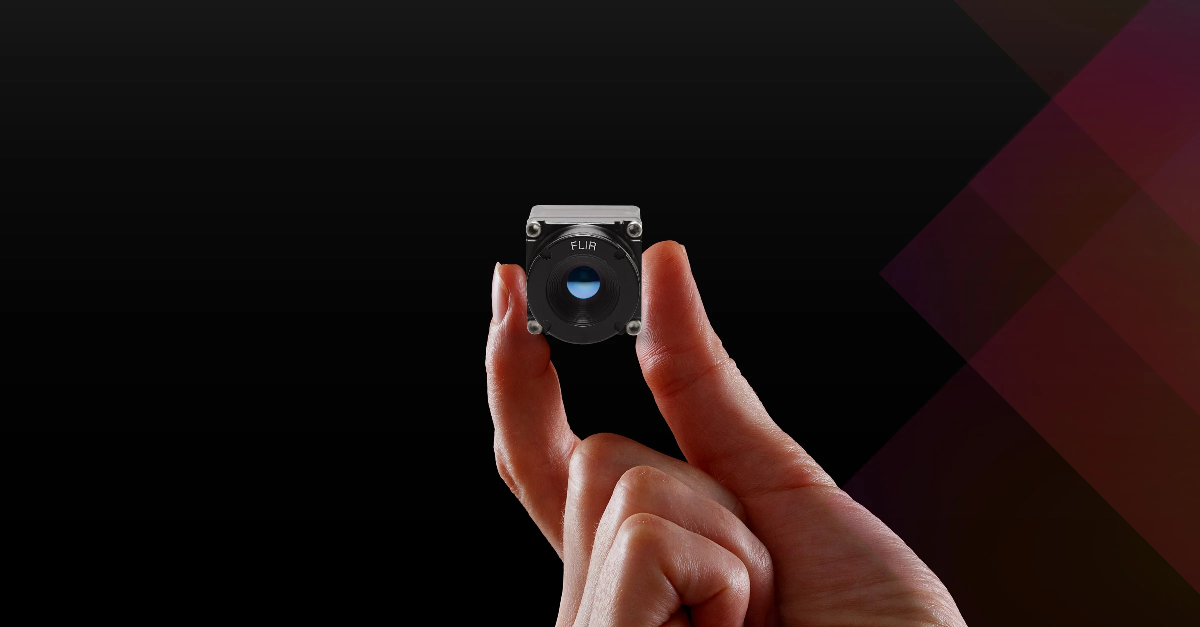
Teledyne FLIR, the Industry Leader, Launches Boson +, a Long-Wave Infrared Thermal Imager Module with an Accuracy of Less Than 20 mK
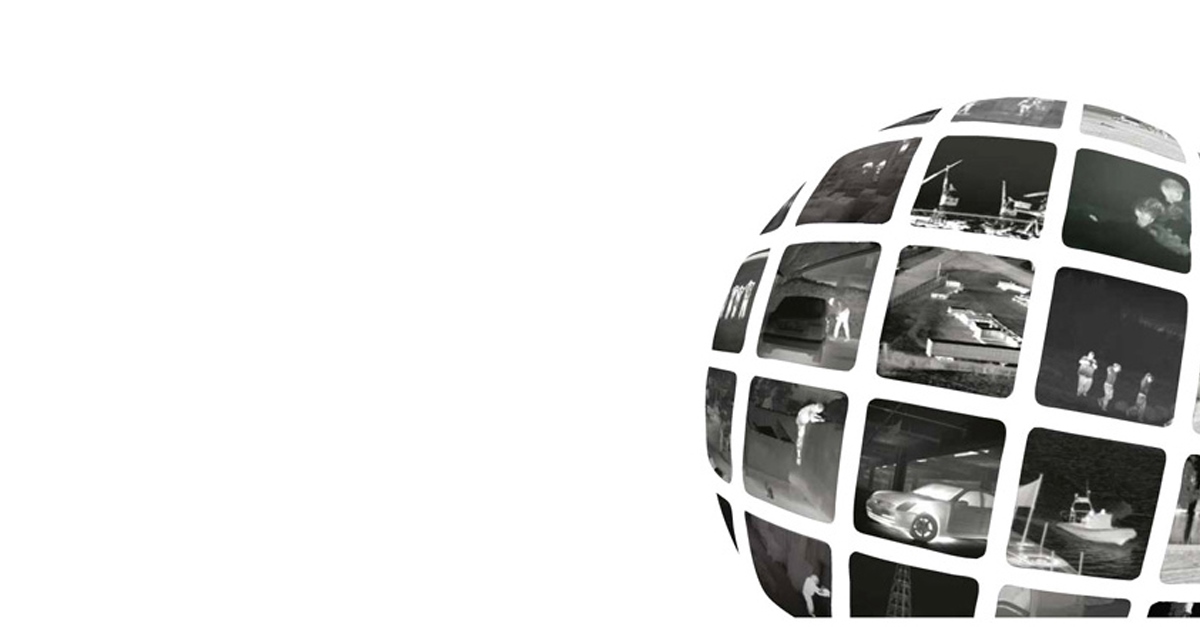
Whitepaper: IP-Based Security Convergence
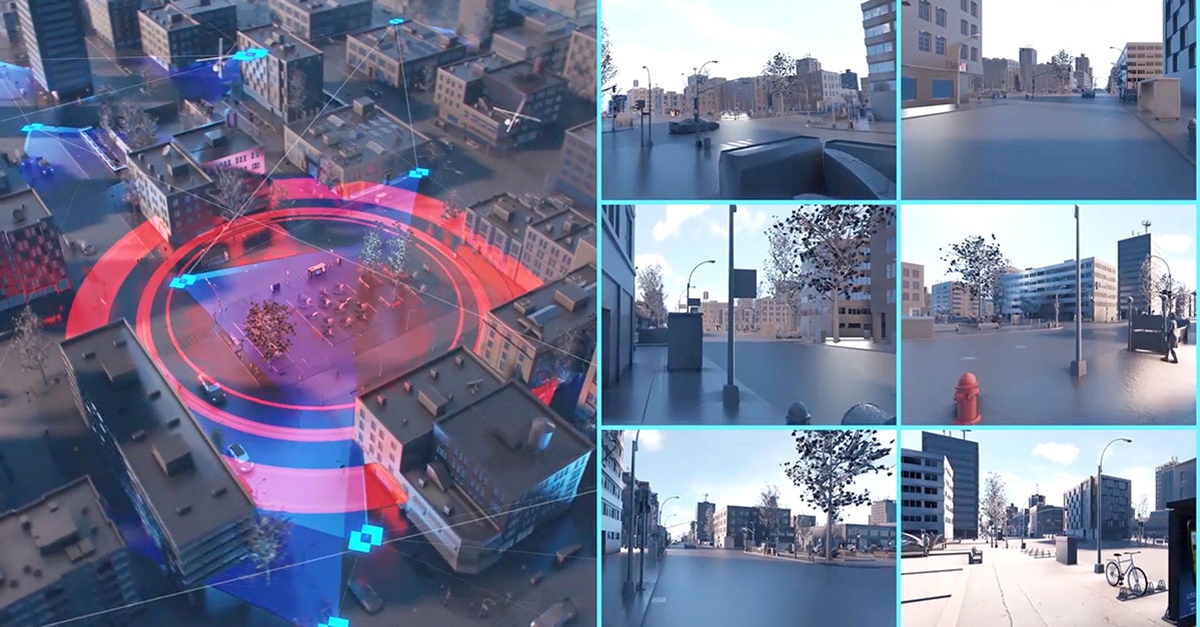
3 Technologies Transforming Safe Cities into Smart Cities
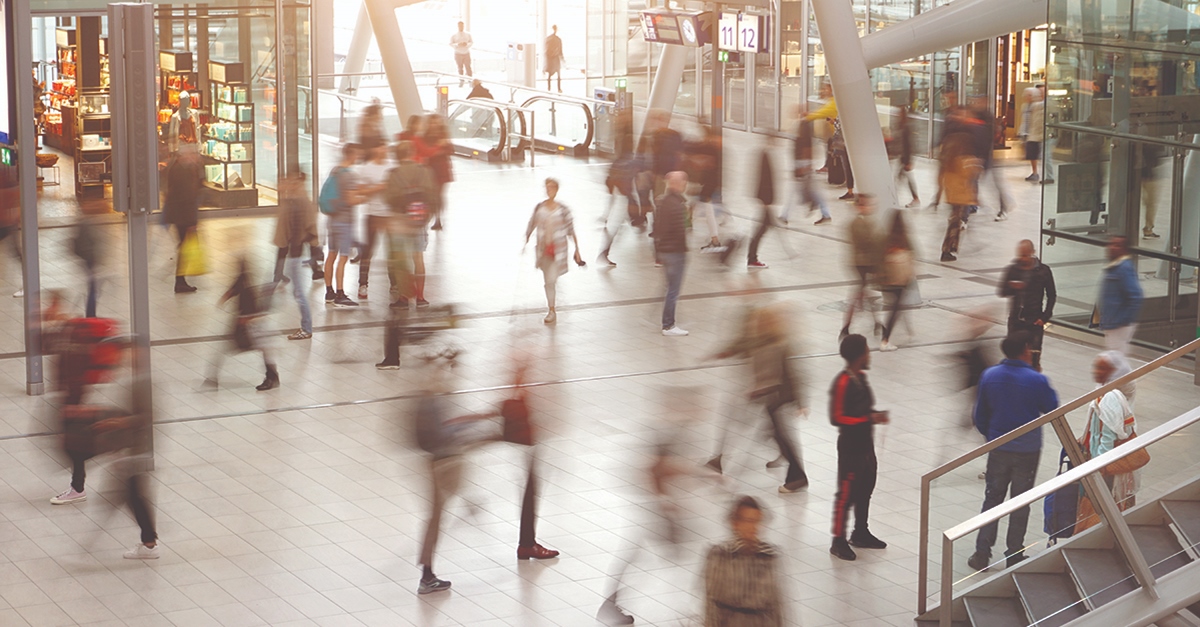
Insights from the Field: Ensuring Workplace Safety Using Thermal Camera Screening for Entry Control
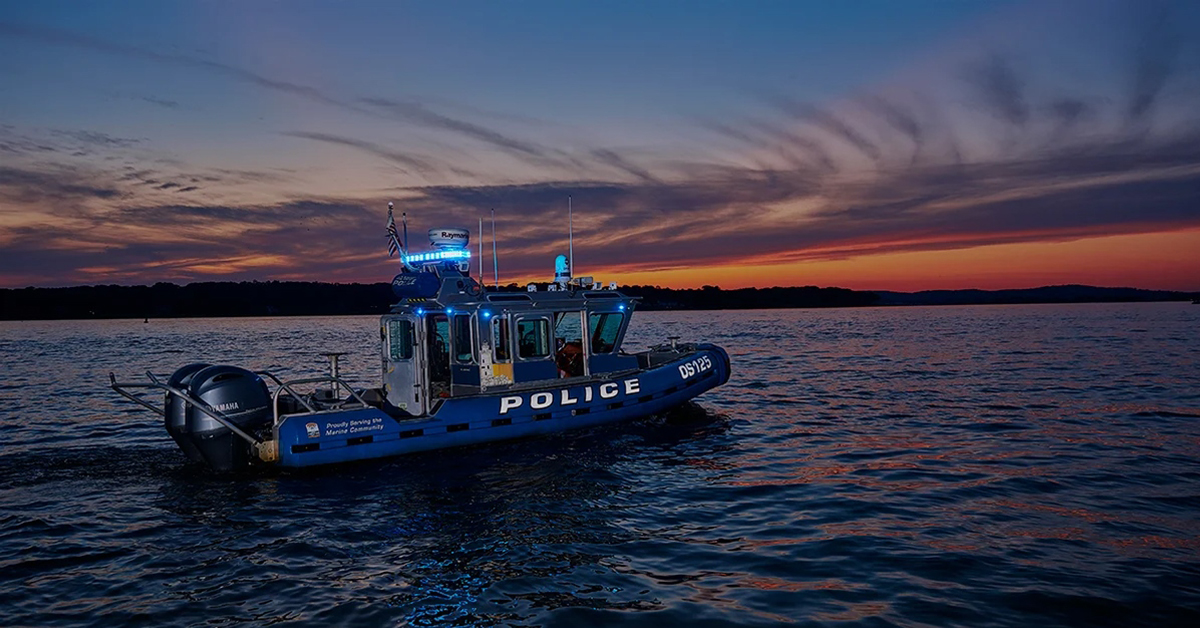
Thermal Night Vision as a Force Multiplier

Can Thermal Imaging See Through Walls? And Other Common Questions
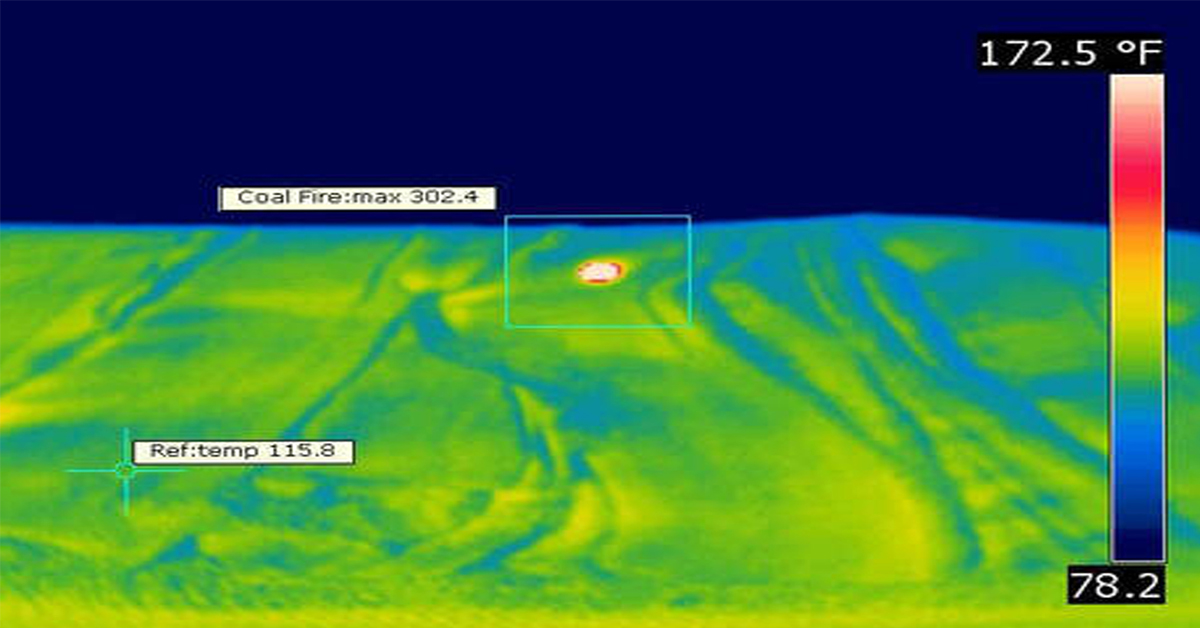
Application Spotlight: Early Fire Detection for Rapid Heat Generation
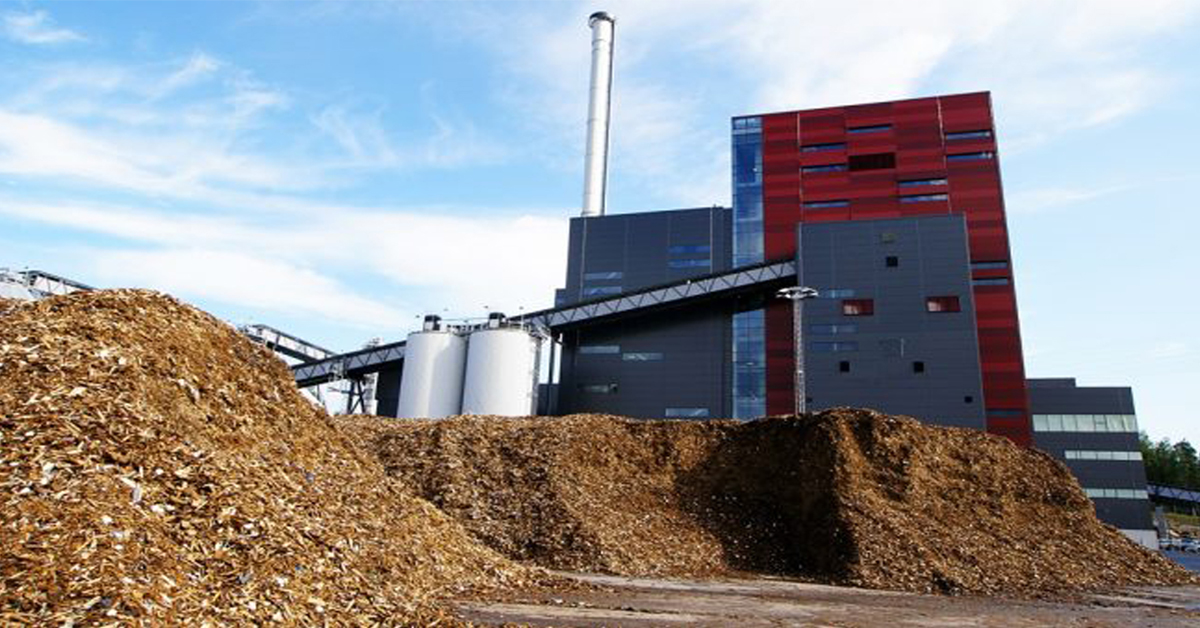
Protect Personnel and Equipment by Detecting Early Signs of Fire
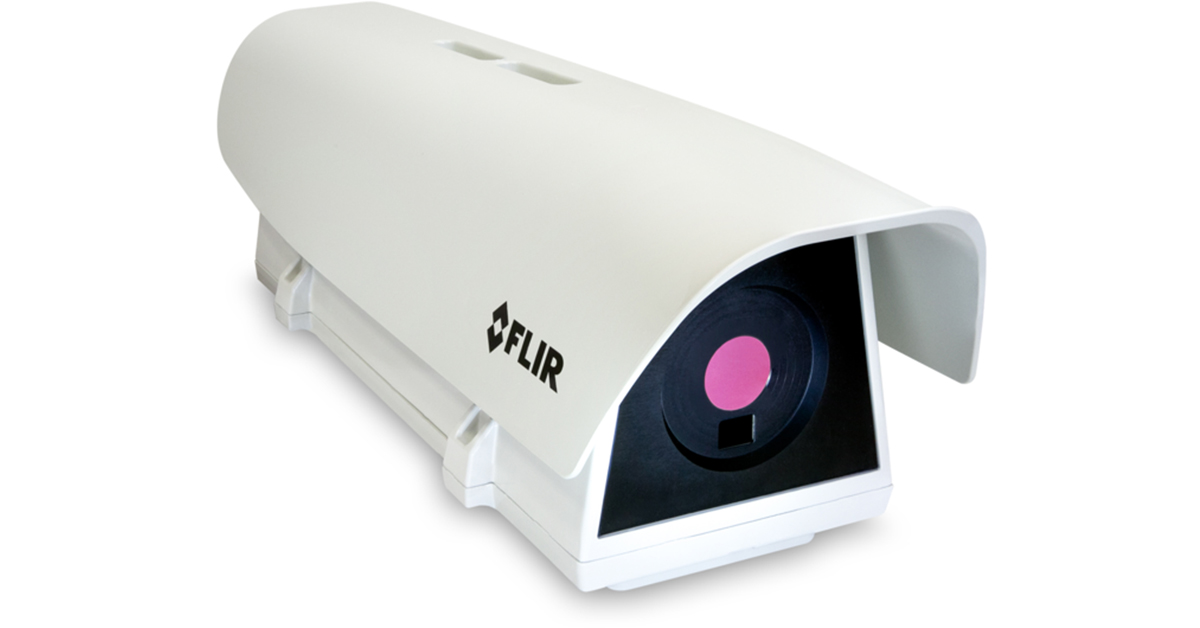
Teledyne FLIR Launches A500f/A700f Cameras for Fire Detection and Condition Monitoring
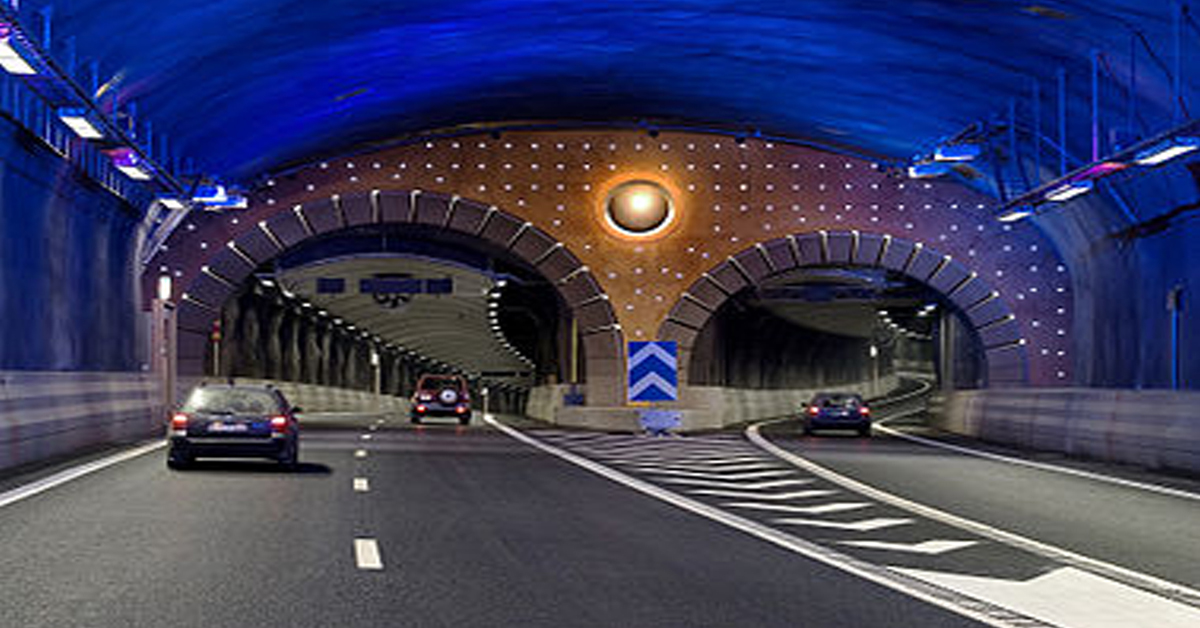
Thermal Imaging Cameras Help Guarantee Fire Safety in Tunnels
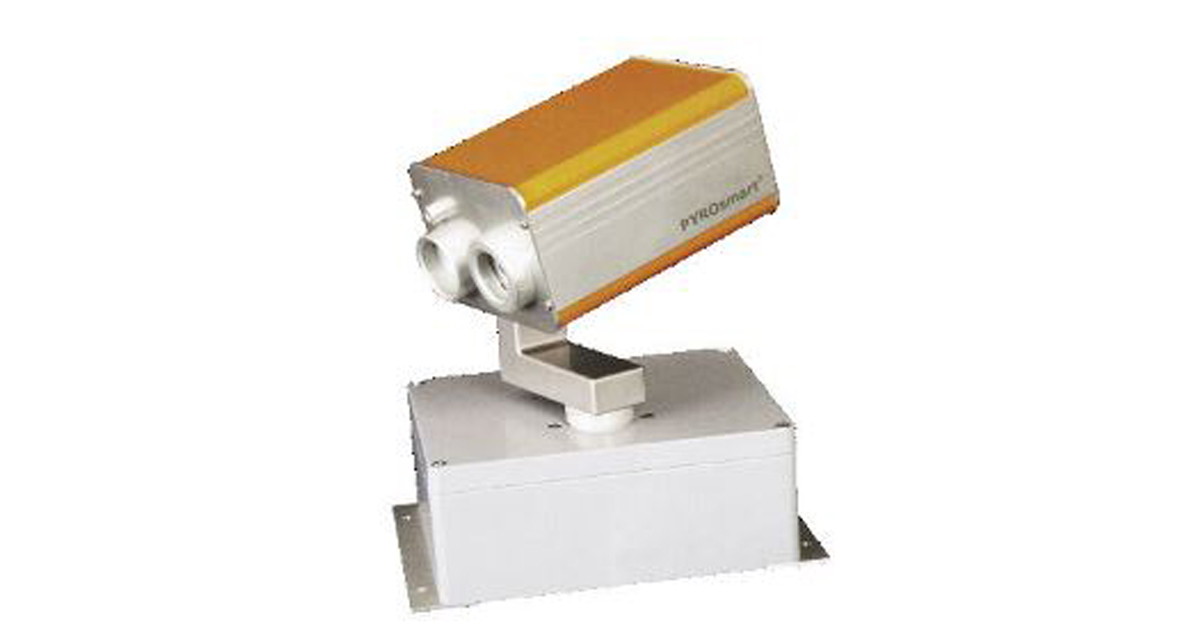
Thermal Imaging Cameras Help to Prevent Fires
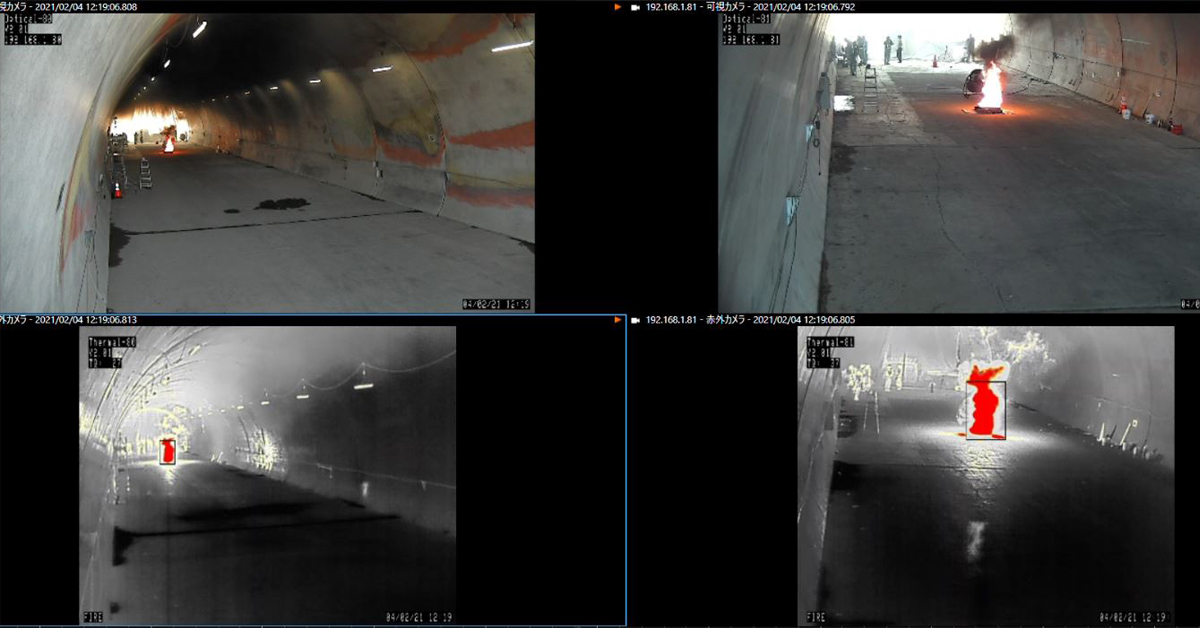
ITS-Series Dual AID Surpasses Standards for Fire Detection Systems in Japan
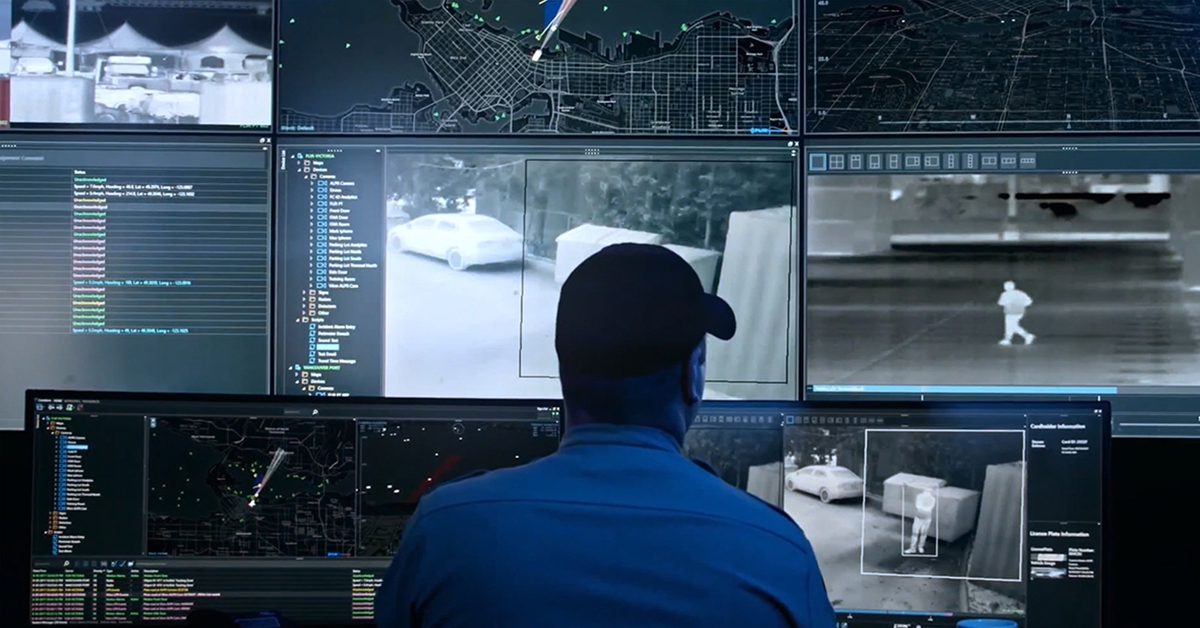
How Layering Multispectral PTZ Cameras and Radars Improve Perimeter Protection
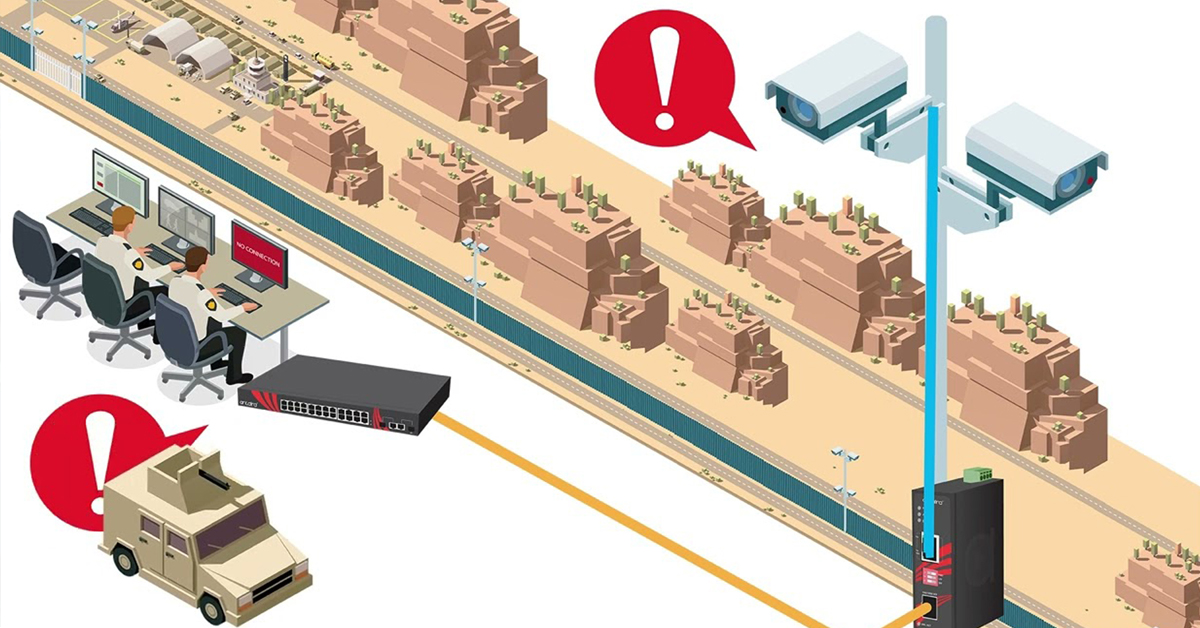
POWER REMOTE RESET TECHNOLOGY - PRRT
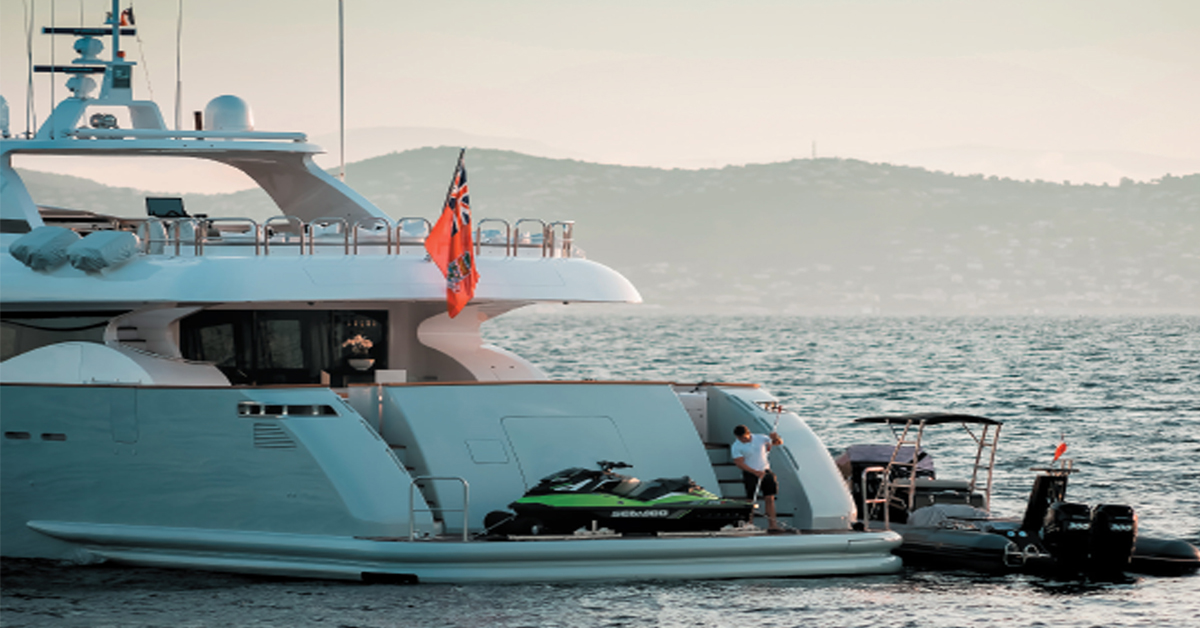
Why Yacht Owners are Adding Thermal Imaging Cameras to Minimise the Risk of Lithium-Ion Battery Fires?
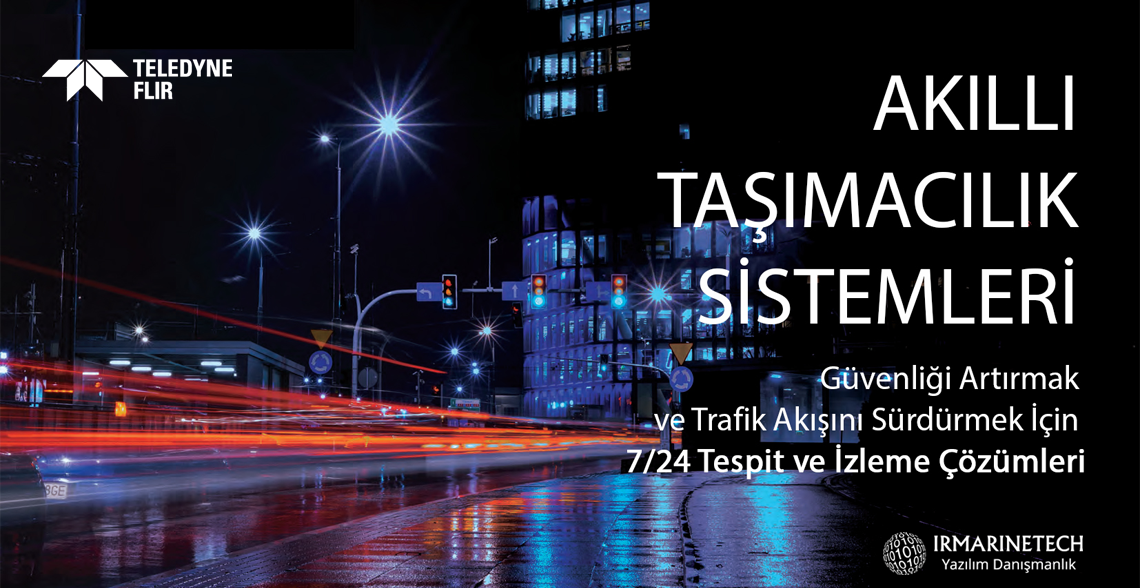
Intelligent Transportation Systems
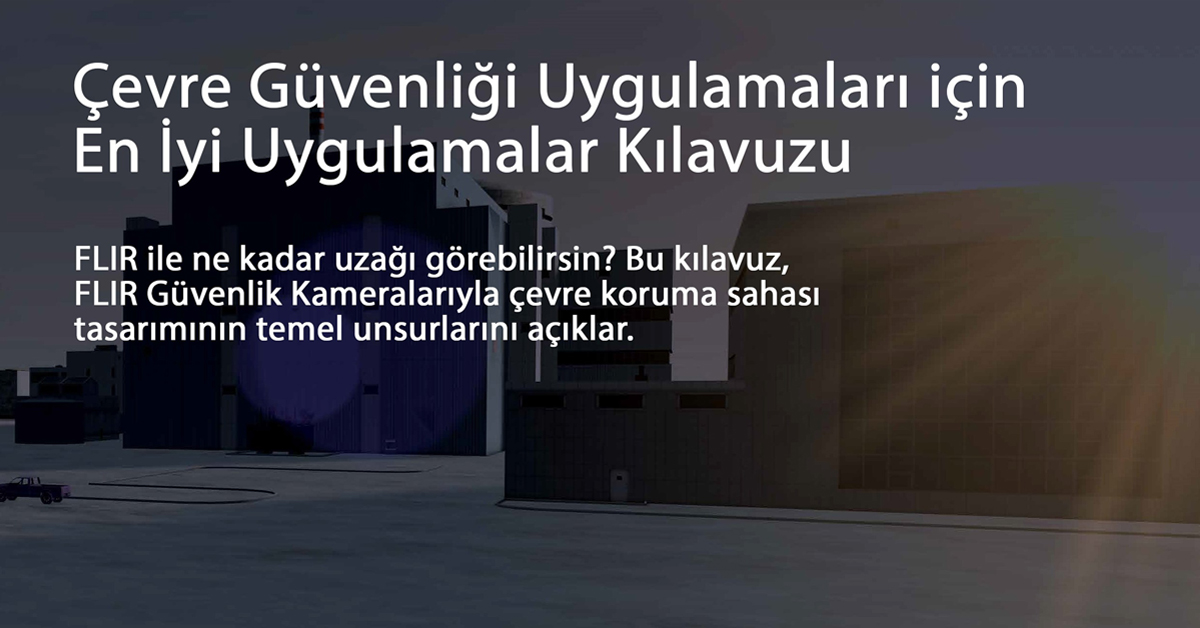
Best Practices Guide for Perimeter Security Applications
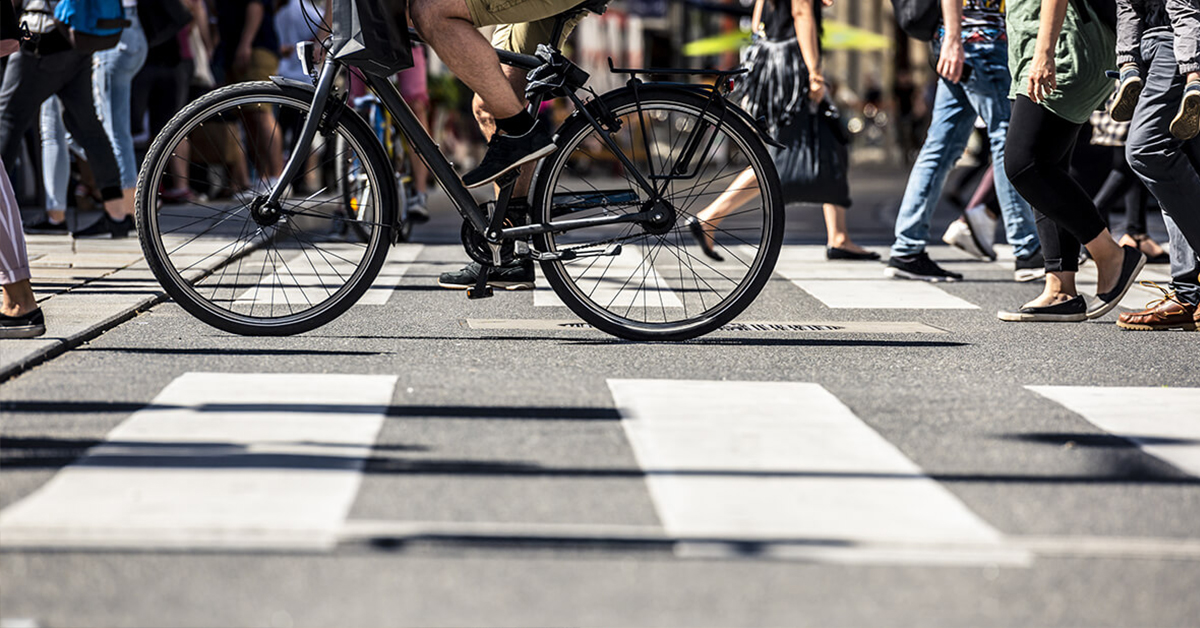
Protect Pedestrians, Bicyclists and More with Thermal Smart Sensors
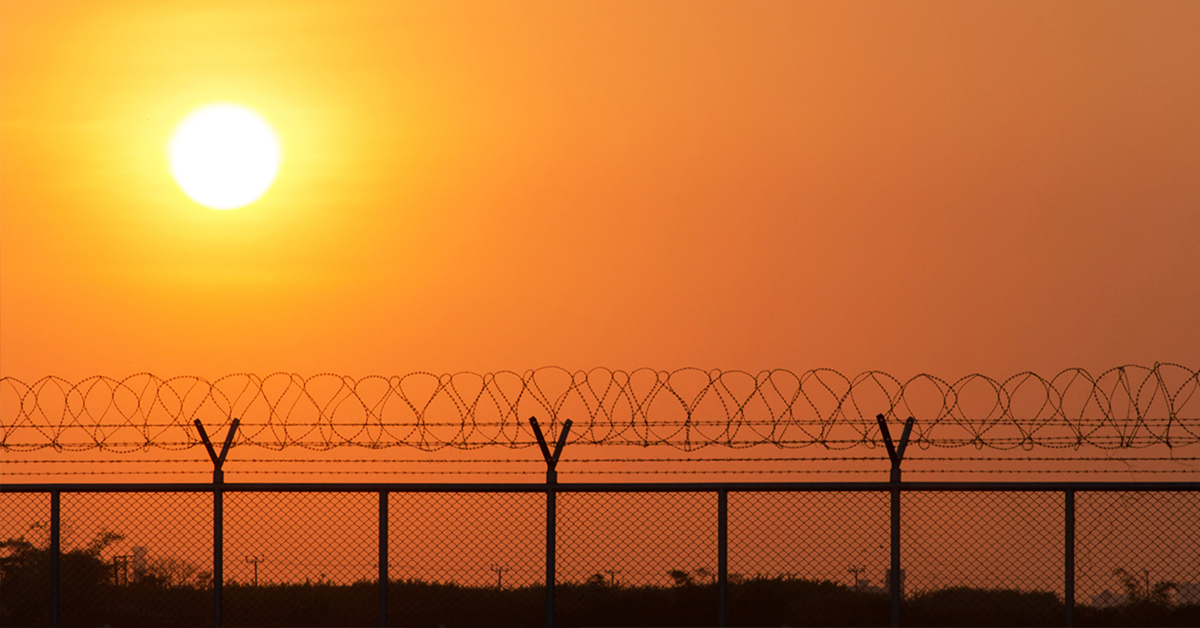
White Paper: Application of Ground-Based Security Radar to Perimeter Systems
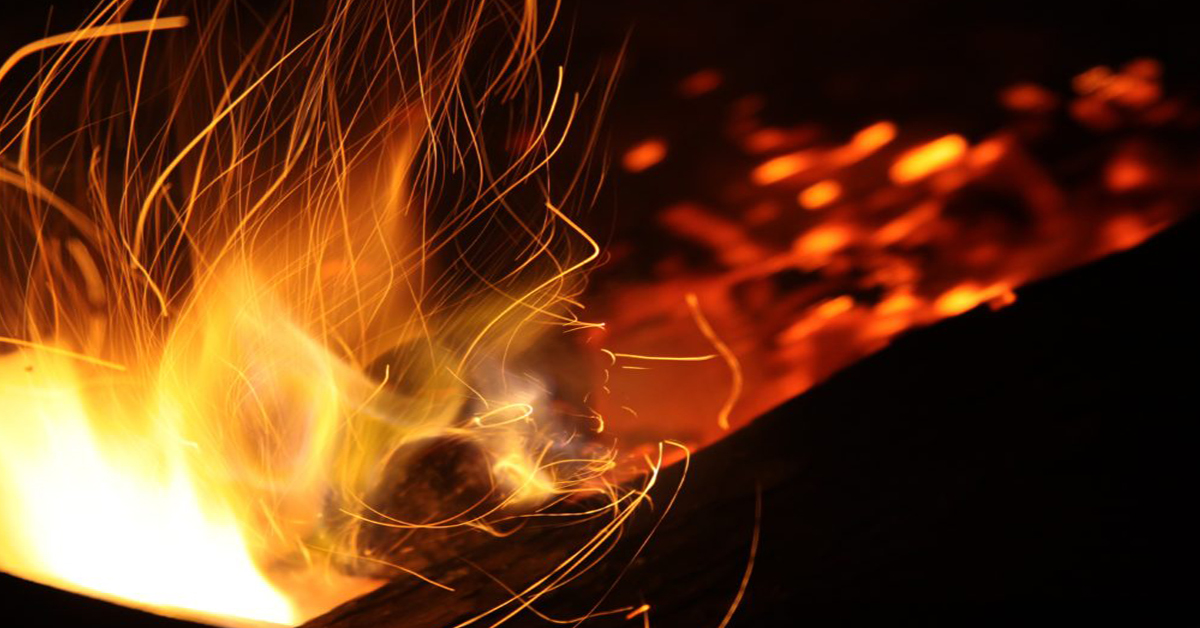
What is Thermal Leakage and How to Reduce Its Risks
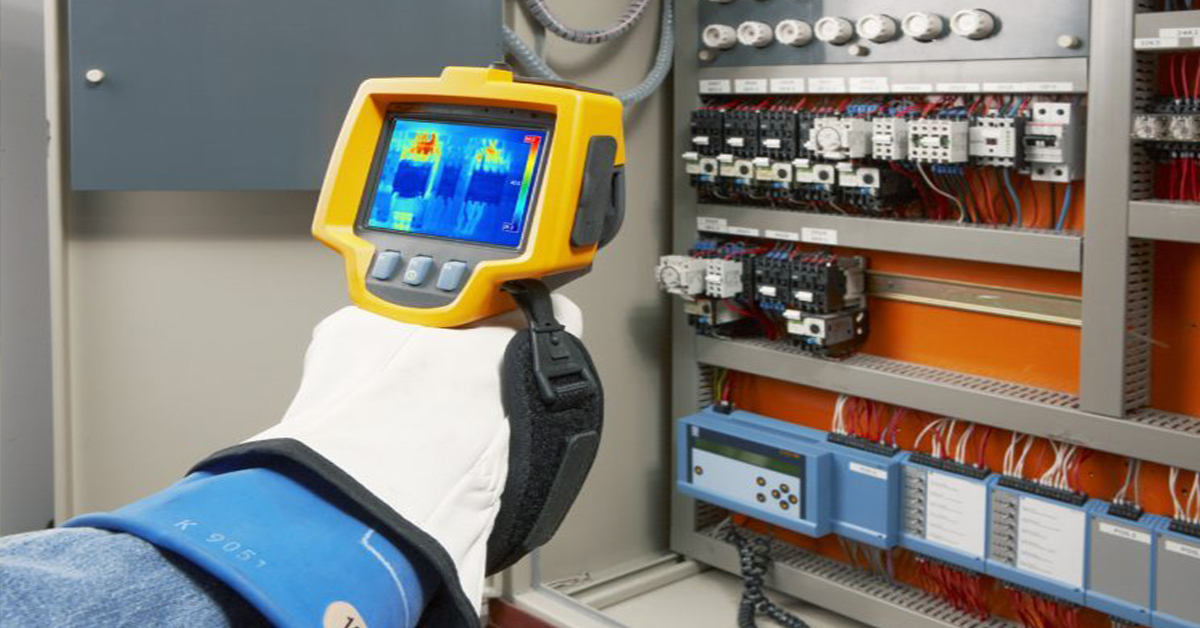
Battery Inspection Using Advanced Thermography
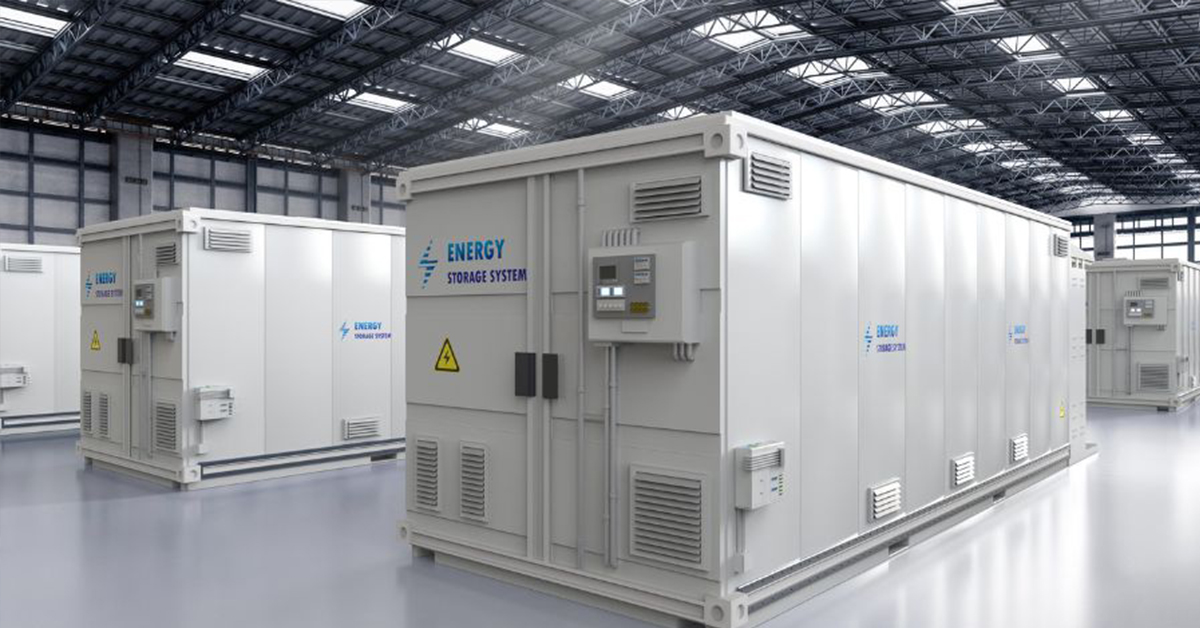
Providing ire Protection for Lithium Battery Storage
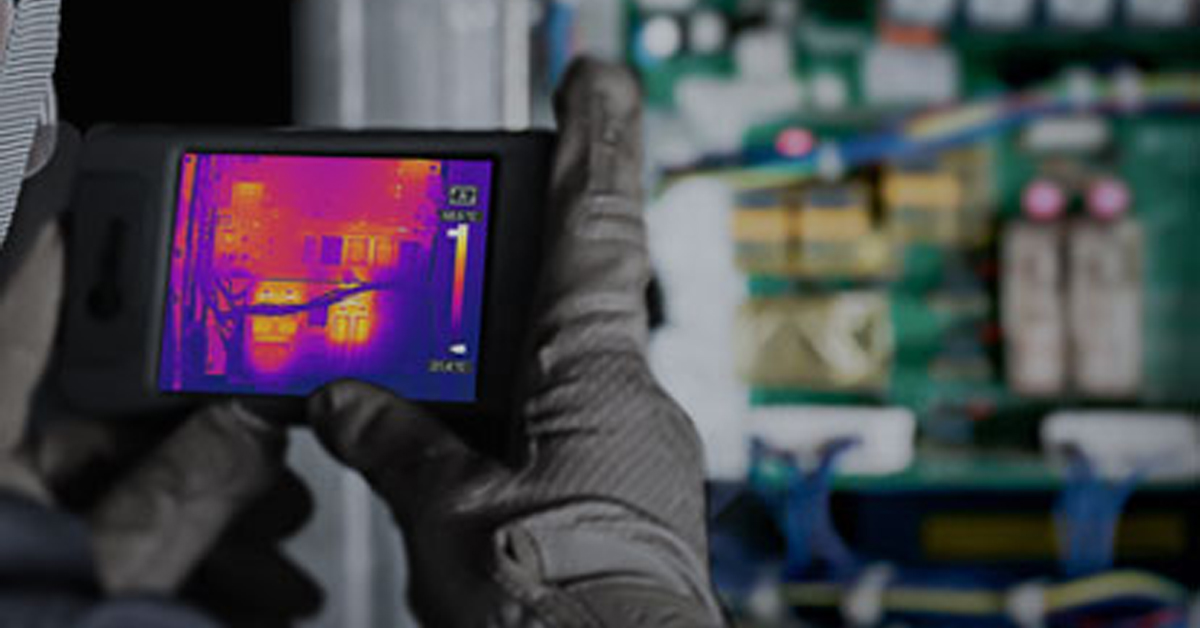
The Power of Thermal Imaging

Why Panel PCs Are Perfect For Industrial Applications?
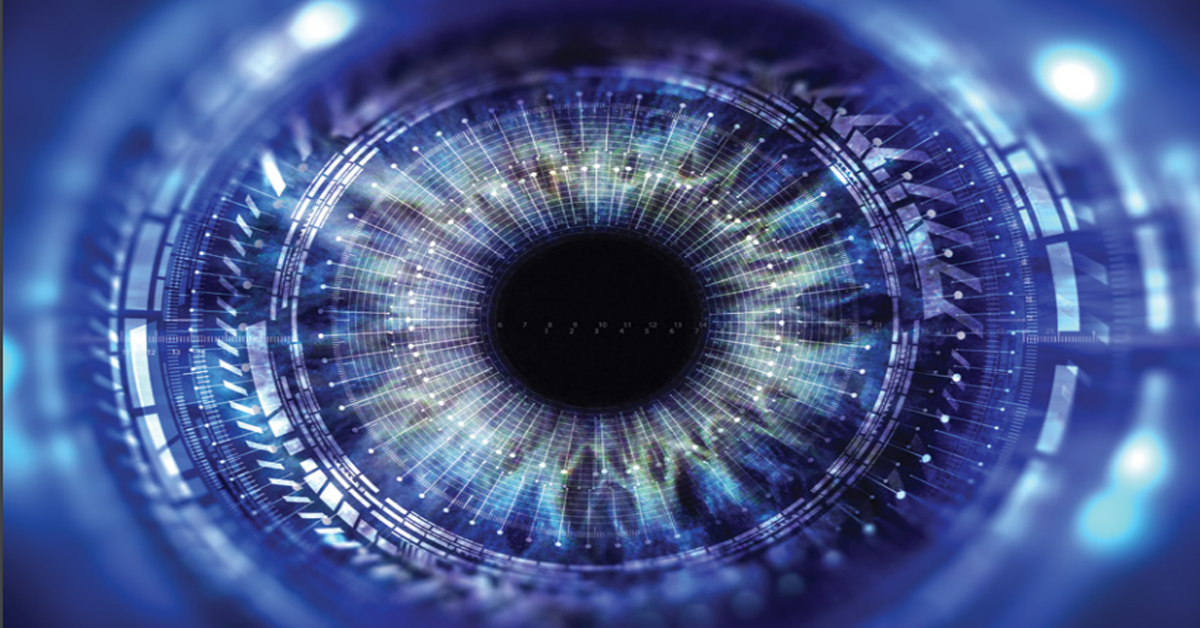
Teledyne DALSA
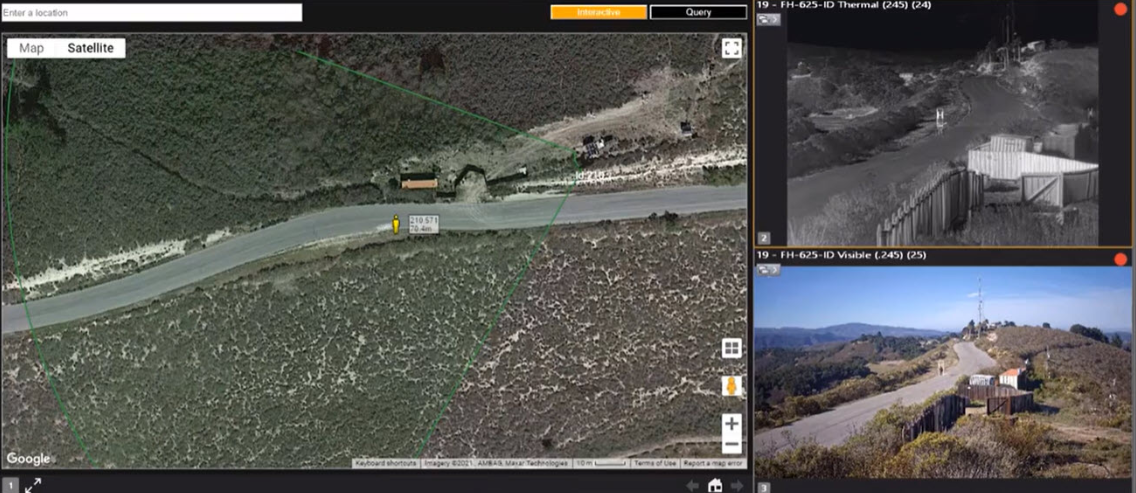
Advantages of Virtual Barrier Video Analytics for Perimeter Security Systems
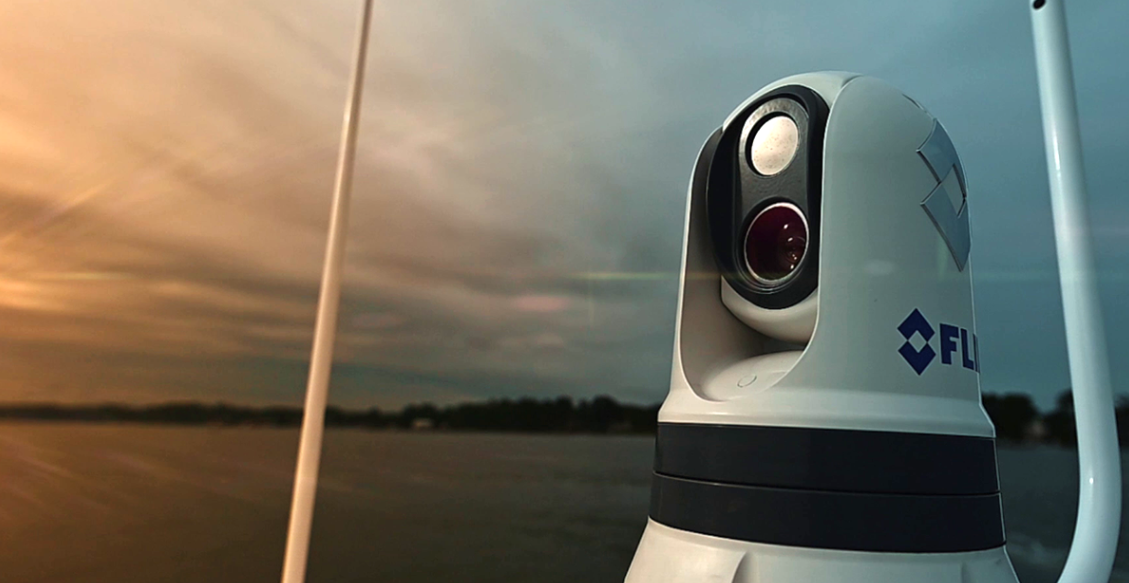
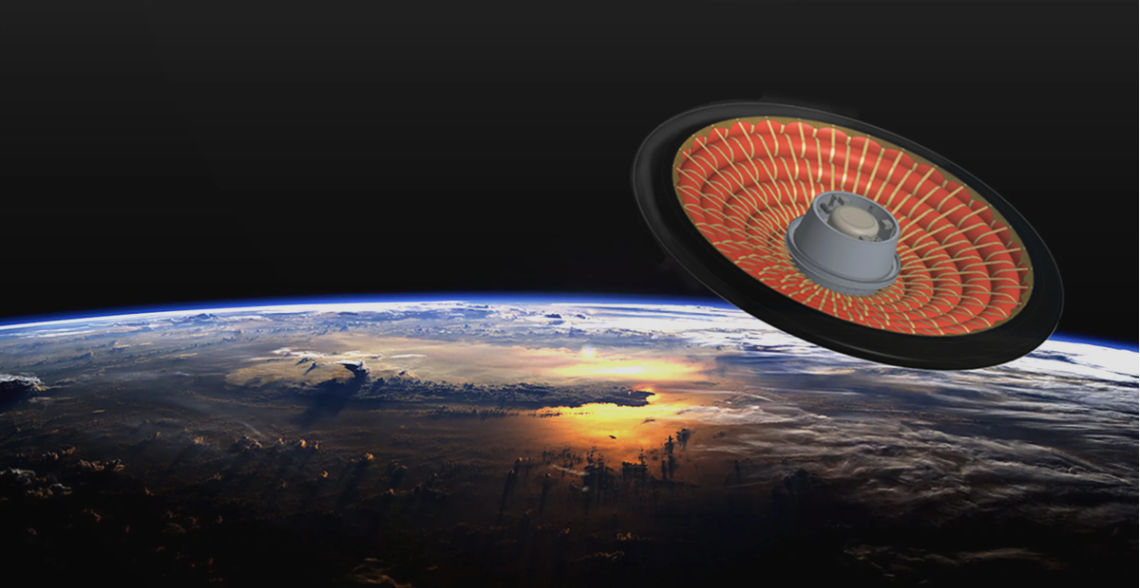
NASA Takes the Teledyne FLIR Boson Thermal Camera Module Out of this World
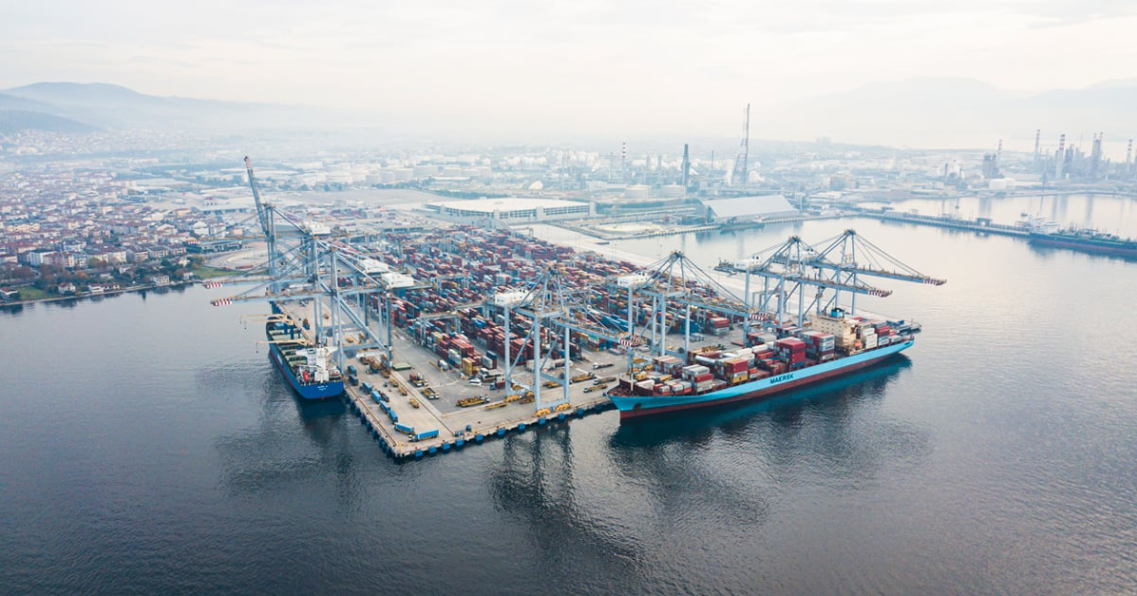
Port Security Enhancement: DP World Yarımca's Trust in FLIR Security Solutions for Effective and Safe Port Operations
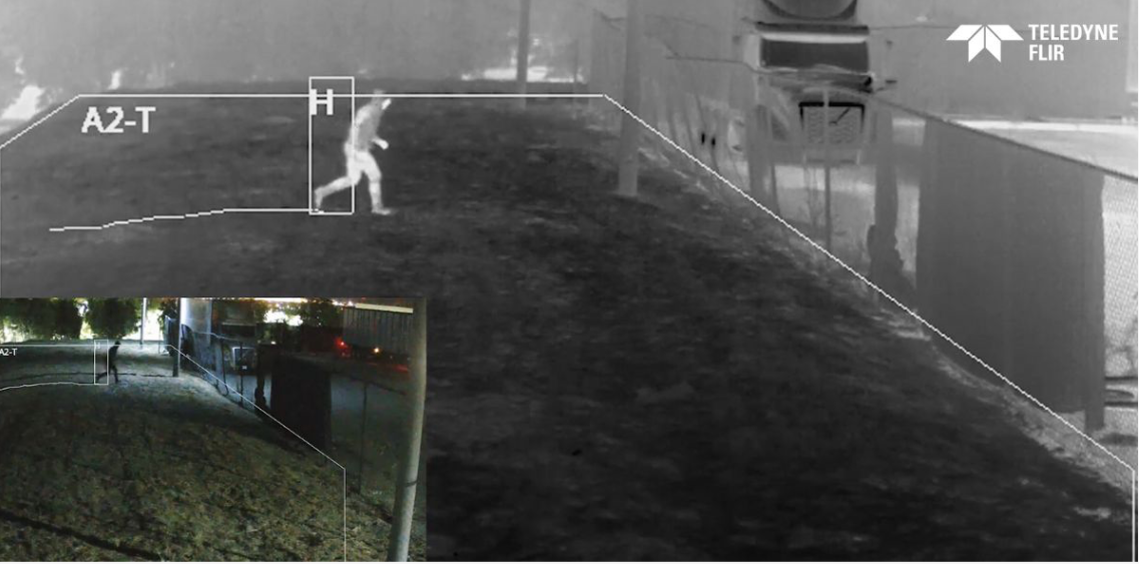
The Importance of Thermal Sensitivity (NETD) for Detection Accuracy
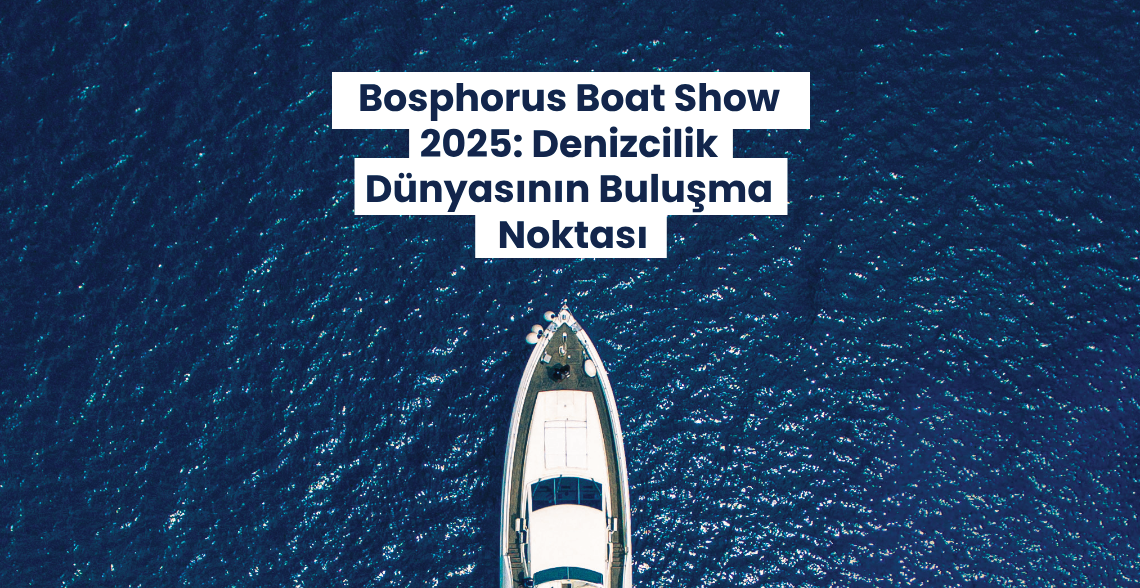
Bosphorus Boat Show 2025: The Meeting Point of the Maritime World
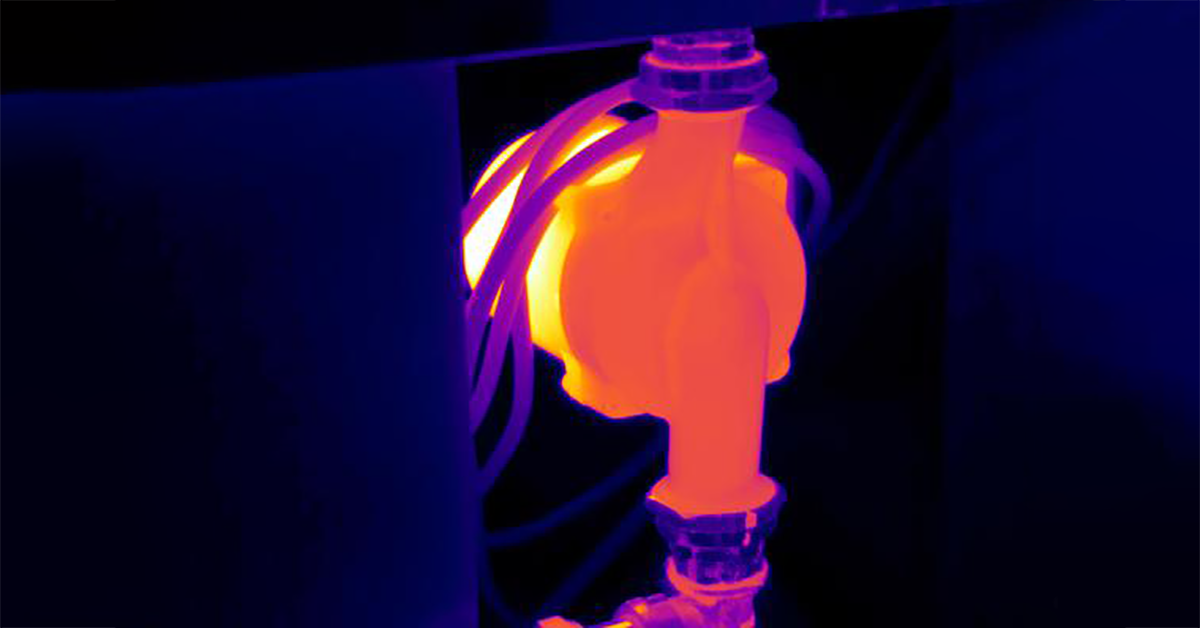